>ブログ
怒涛の6/12(土)‼ 旧マシン修理~ファイバーレーザー溶接機導入の話(=゚ω゚)ノ✨
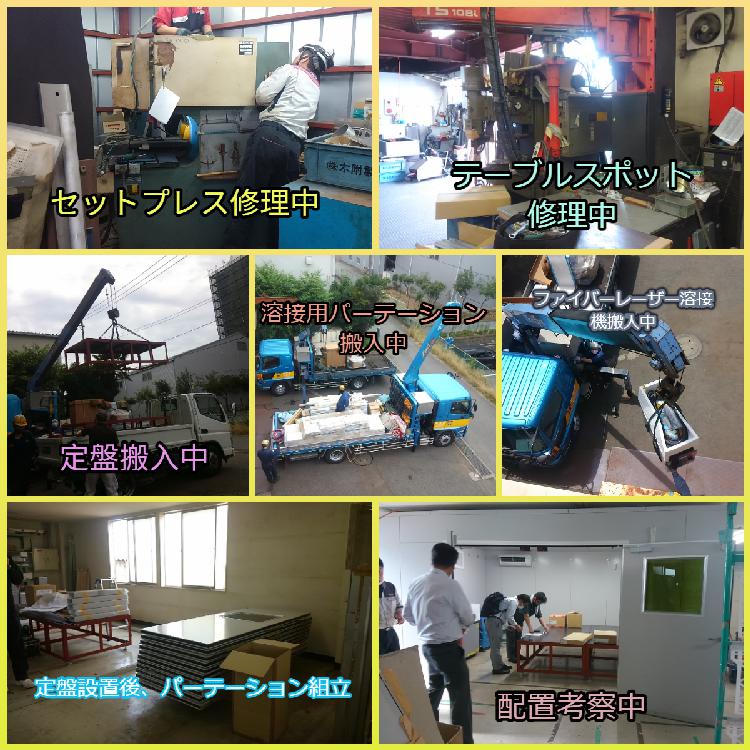
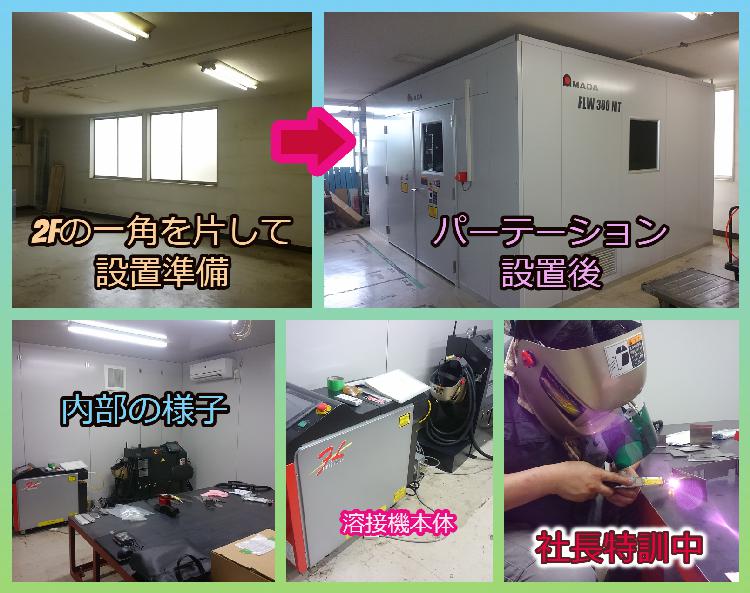
え~
大変、大変ご無沙汰しております!
m(__)mm(__)mm(__)m←(一年分の謝罪)
約1年程ブログの更新が出来ず今日に至りました。
この間、色々とご報告したいお話もあったのですが
中々時間が取れず写真ばかりが溜まっております(-_-;)
ですが当方の中で
『これは載せない訳には行かない大ニュース!』
な出来事でしたのでなんとか時間を作りお知らせしたいと
夜中3時では有りますが自宅にて更新しております(^^;)
ひと月程前の6/12(土)、会社の休みに合わせて機械2種類の修理と
ファイバーレーザー溶接機の設置を同時に行いました。
稼働日ですと中々機械を止められませんし、社内がワサワサしますので
こういった大きな作業は大体、お休みの日になります。
前日から用意が始まって、当日は朝から色んな業者が入れ替わり立ち代わりで、
翌日にまで持ち越してなんとかかんとか終わったと言った感じです(^^;)
ピーク時には弊社内の駐車スペースでは車が収まらず
お隣の会社にも車を停めさせて頂く事となりましたm(__)mアリガトウゴザイマシタ
【出入り業者と車の数 ※敬称略】
(修理の部)
●セットプレス修理、スポット溶接機修理班 (AMADA)2台
(ファイバーレーザー溶接機設置の部)
●立ち合い、セットアップ等 (AMADA)3台
●ガス配管工事 (田邊ガステクノ)2台
●窒素配達 (田邊ガステクノ)トラック1台
●機械搬入(重量物取り扱い) (関本組)トラック2台
●定盤配送 (辻岡溶剤店)トラック1台
●パーテーション設置 (AMADA手配業者)2台
●電気配線、空調設置 (千葉電機)1台
●その他導入に伴う関連会社
等々・・・・
そんなこんなで修理、ニューマシン導入、周辺機器等で・・・
かなり高額の出費となりました・・・(^^;)💦
ハッキリは言えませんが、当方の住む地域で家が1件買える程です(;^ω^)
通常TIG(アルゴン)溶接機で100万円位します。
その〇〇倍以上するファイバーレーザー溶接機の実力とは・・・
導入に踏み切った経緯、
ファイバーレーザー溶接機導入のメリット等、
近々詳しくお話しできれば良いなと思っております。
本日は取り急ぎご報告まで!
ではまたお会いしましょう(・ω・)ノ
投稿: 2021/07/11
奪還計画パート2(スーパー金型編(^^;)
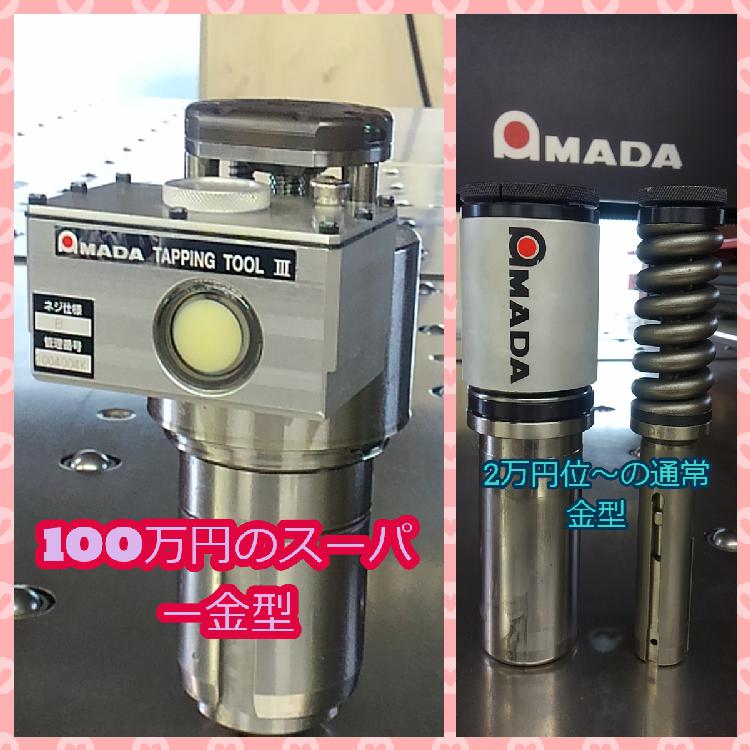
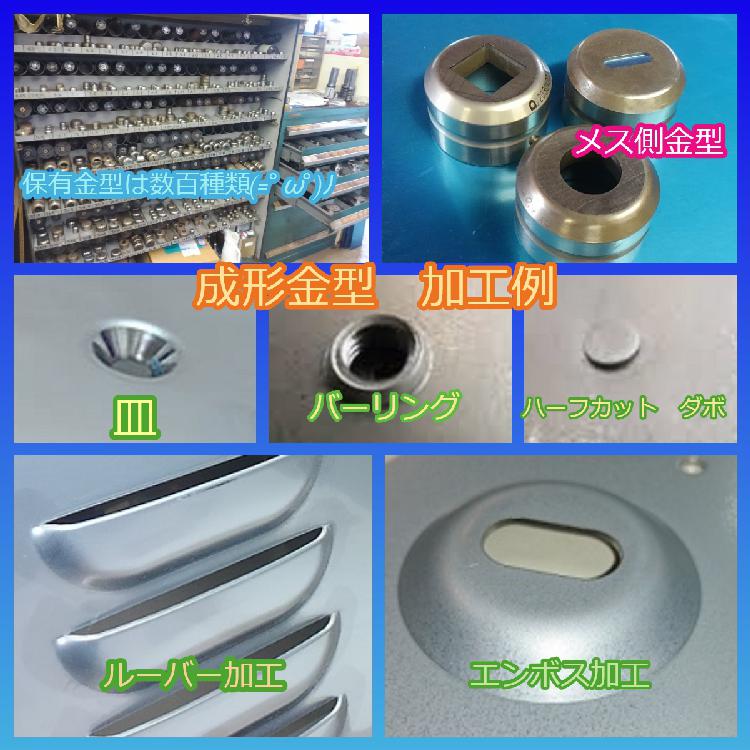
え~
6月に入り今年も半分を過ぎようとしておりますが
『コロナ渦』も少し落ち着いて来たようで
緊急事態宣言も解除されましたね(*'ω'*)
・・かといってまだまだ油断せずに気を引き締めていかねばと
弊社でも玄関に『アルコール消毒液』を設置したり
従業員にマスクの配布をしたり、出来る限りの時短勤務に取り組んだりしております('ω')
さて、話は変わりますが前回の
『テーブルスポット修理代奪還計画』に引き続き
新たな『奪還計画』が始まりました(^^;)
今回は『スーパー金型導入費奪還計画』です(^^ゞ
一枚目、左側に写っている金型が、今回購入に踏み切った
タレットパンチャーで使う『タッピング金型』です。
(※写真はクリックで拡大できます(*'ω'*)b)
名前の通りタレパンで製品をブランク加工する際に『タップ』を切ってくれる金型です。
普段は『タップ』がたつ箇所の下穴を開けるだけの加工をした後
ボール盤やタッパーを使い人力でタッピング作業を行うのですが
この金型を使えば、ブランク工程中、下穴加工をした時に
タップも同時にやってくれるという優れものなんですっ( `ー´)ノ
『なんだぁ、普通じゃん( 一一)・・・』
なんて声が聞こえてきそうですが・・・
この金型・・・導入するにあたり
セッティングに関わる作業や、関連部品、メンテナンスに関わるケミカルも込みで
なんとトータル『100万円』程かかるんですっ(。-`ω-)ムム…
『タップ位、人力でやればいいじゃん(*´з`)』
と、思われる方も多いでしょう…(;´∀`)…
いや、実際弊社内でもそう言う意見も多く
導入に至るまでには結構な時間を要しました(^^;)
まぁ、実際これまでウン十年、すべてのタッピング作業は人力で行ってきたのですが
ここ最近、量産品の受注も増えてきまして・・・
例えば『M5』のタップが18箇所ある製品を500個位
定期的に受ける事も有ったり(^^;)…
普通に計算すると『M5』が9000箇所という事になります(^^;)
実際、これまでそれを人力でやっていた訳なんですが
少数精鋭で回している弊社にとっては
誰か彼か現場で何かを担当している職人さんが『タッピング作業』に
1日以上囚われているという事態に多々直面し
ほかの作業が滞る恐れも出てきたので
色々と健闘した結果、今回思い切って導入に踏み切る事にした次第であります(;'∀')
タレパンがタップを代行してくれている時間に
職人さんは他の仕事をどんどん進められるので
金型を導入した一時的な出費は痛いですが
『金型代奪還』への道はそう遠くないっ!と思っております( `ー´)ノ
前出の品物、M5の他にも『皿加工(平ネジを閉めた時、頭が出ない様にするザグリ)』が
何箇所か有り、そちらも特注金型を使用してタレパンで加工しています。
板厚も3.2㎜なのでレーザーで外形を切るより
タレパンでガンガン抜いたほうがはるかに速いので、かなりの時短となっております(*'ω'*)
近年、弊社で製作する品物は『少量多品種』になってきていて
割とレーザーで加工する物が多くタレパンが稼働しない日も多々ありました。
しかし『量産品』やレーザーでは出来ない『成形加工』のある品も受注する機会が増えてきたので
今では
『若いもん(レーザー7歳)にはまだまだ負けられんっ( `ー´)!←(タレパン20歳越え)』とばかりに
タレパンもかなりの稼働率で頑張っております(*'▽')
『成形加工』とは・・・(2枚目の写真をご覧ください)
ダボ出しやルーバー、エンボスやバーリング、皿など…
簡単に説明しますと金属の表面に凹凸をつける加工です('ω')
その形状にあった金型をセットし押し出して成形します。
弊社では多くの金型を保有しており様々な形状の成形加工を行っております(*'▽')
個々のお客様の御要望に応えられるよう、年々金型の数も増えてまいりました('ω')
量産品であれば、特注金型を作ってオリジナルな成形も出来ますので
『こんな加工出来ないかな~』などありましたら是非ご相談下さい!
まだやったことは有りませんが『💛型』『★型』なんかのエンボスが有ったら楽しいですね( *´艸`)←妄想中
では本日はこの辺で(=゚ω゚)ノ
投稿: 2020/06/14
テーブルスポット修理の話🔧
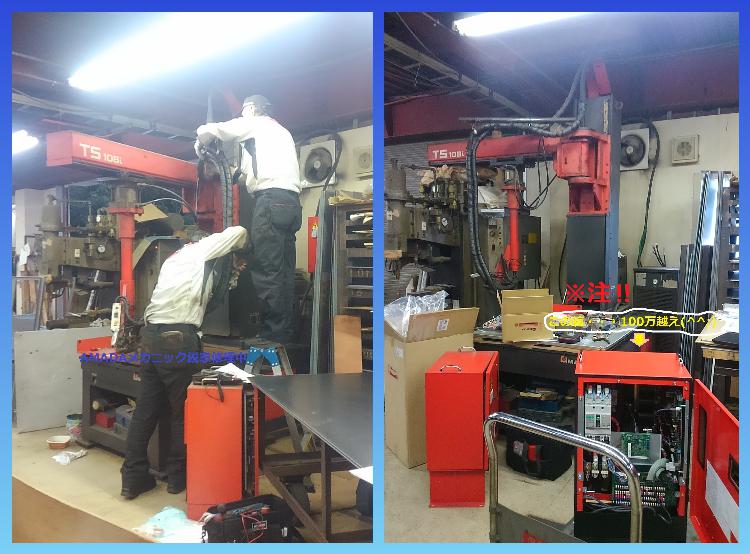
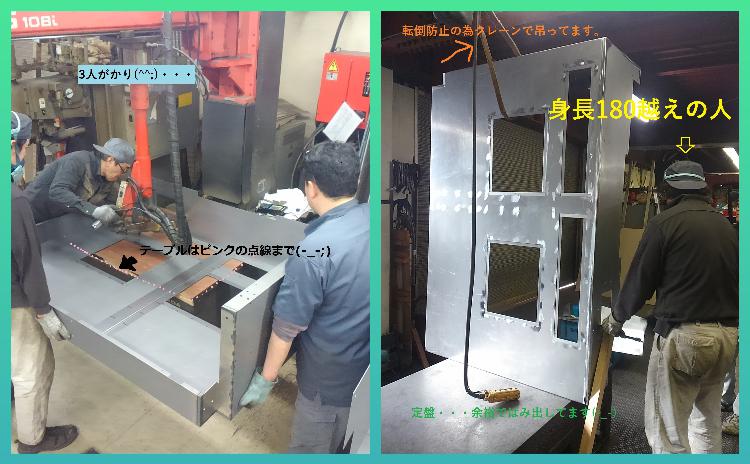
え~
ちょっと前の話になりますが
弊社のテーブルスポット溶接機を修理致しました。
だいぶ前から調子がイマイチだったのですが
他にも足踏み式スポット溶接機が3台ありますので
そんなに困る事は無かったし
本気で直すとなると結構金額も張ってしまうので
『そのうち直そう』『今度直そう』『機会が有ったら直そう』と
どんどん後回しになっておりました^_^;
しかし、ここの所色々な種類の製作依頼が有ったりして
やはり『テーブルスポットがちゃんと使えないと不便だ‼』との声が高まり
今回思い切って直す事になりました(^^;)
・・・修理代は工賃込みで100ウン十万円を超えました(*_*;
一時期、新しい物に入れ替える事も検討しましたが
それなりの物を買ったら軽く1000万円以上するので
修理をする事を選びました(^^;)。
それでも・・・100万円の売り上げ上げるのって結構大変です(^^;)
かくして
『テーブルスポット修理代奪還計画』が始まったのですが・・・
2枚目の写真をご覧ください( ̄ー ̄)・・・
『いや、それ、ウチの仕事じゃ無いんじゃね(◎_◎;)?』と
当方も思わず社長に言った程デカい品物の製作を請け負う事になりまして(^^;)・・・
まぁ、やってやれない事は無かったのですが、
テーブルスポットのテーブルや溶接の定番に乗り切らない程の大きさで
品物が落ちないように3人がかりで支えながらの作業になりました^_^;
数も8台位あったので、出来あがっても置く場所に困るしで、
ちょっと大変な品物でありましたが
この仕事も『テーブルスポット』が無ければ受けられない品物でしたので
充分『修理代奪還計画』に貢献はしてくれました!
修理前までは受けるのをちょっとためらっていた製作依頼も
今ではガンガン受けれるようになったので
着々と修理代奪還に向け頑張って行こうと思います(^^ゞ
では本日はこの辺で!
投稿: 2020/04/19
木附製作所2020年度年間休日カレンダー(予定)とコロナウィルス
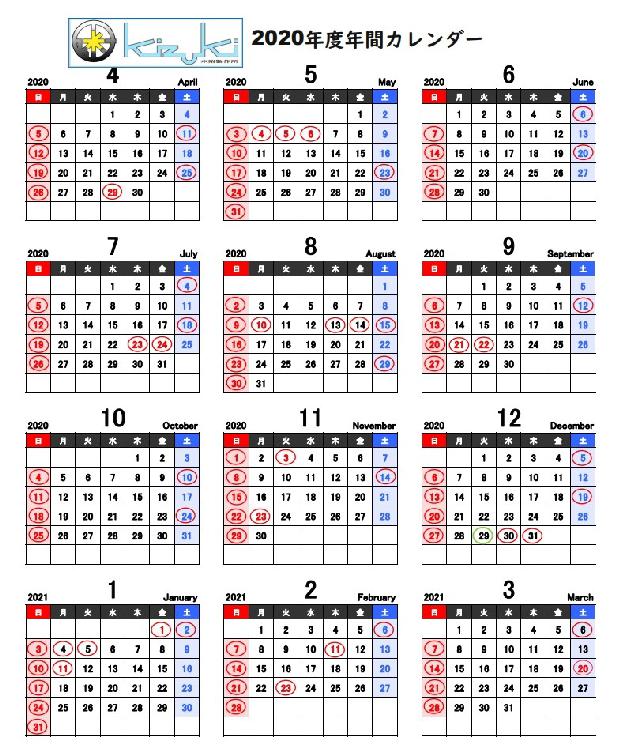
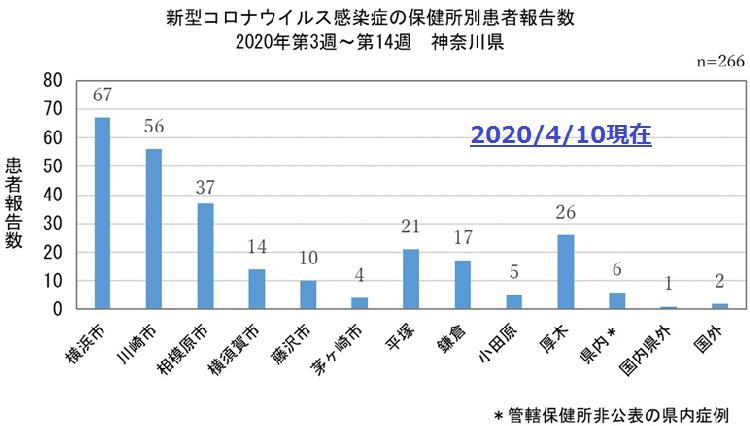
御無沙汰しておりますm(__)m
3月まで怒涛の忙しさでHPの更新もままならず今日に至ってしまいました。
4月より新年度となりましたので、年間休日予定を掲載させて頂きます('ω')
・・・
まぁ、毎年そうなのですが、あくまで予定です(^^;)
忙しければ土曜も日曜も稼働するし
暇なら出勤予定日でもお休みします('ω')
・・・割と当方と弊社社長は
年間で360位日会社にいるような気がします(^^;)💦
さて話は変わりますが
今、世界中がコロナウィルスの影響で大変なことになっていますね(;´・ω・)
我が神奈川県も緊急事態宣言の対象となりました
しょっぱなから諸に打撃を受けている飲食業や観光地などの宿泊業などに比べて、
弊社のような金属加工業はまだ大ダメージをうけてはいませんが、
徐々に、その悪魔の足音が近づいて来たような気配も感じています。
・・・
実際、8月まで決まっていた仕事に『待った!』がかかりました(-_-;)
正直言って当初は、恥ずかしながら
『世界中の研究者がすぐに薬を作って、割と早いうちに終息に向かうだろう』
なんてまるで『対岸の火事』のように軽く考えていました(-_-;)←反省中
しかし段々に感染者の数が増え、
子供のころから馴染みのある芸能人の方が亡くなったりして
『これは本当にヤバイ!』と感じました(-_-;)←遅い!!
・・・本当に未曾有の事態で全く先が読めず、
今後どう動いて良いものか困惑しております(-_-;)
この騒動が収まるまで少なくても1年半はかかるのではないかとか
被害の甚大なアメリカでは7月位から大恐慌に襲われるのではとか聞きますと、
この日本でも、どれだけの会社が持ち応えられるのか・・・
この先、この騒動が終息するまでの長い先の事もしかりですが
今現在、弊社のような金属加工業は休業要請も来ていません。
政府の言う『出勤者の最低7割削減』も製造業ではかなり難しいのが現状です。
自宅にレーザーやベンダーを持ち帰る事は到底不可能ですし
『この騒ぎが収まるまで何も作らん!』となると
すでに数か月先まで発注のかかっている仕事を放りだし
お得意様に迷惑をかける事になってしまいます(-_-;)・・・
それ以前に会社がストップすれば従業員の収入もストップしてしまいます(._.)
仮に保障や援助があれば潔く休むのかと聞かれても
『はい!』とは即答できないような気持ちです(-_-;)
この渦中の中、スーパーやコンビニ、医療関係者の方々が一生懸命働いてるのを見ると、
なんか働かないでお金を貰うのは申し訳ないような・・・(-_-;)
サービス業や医療関係者、バスの運転手さんとかは
毎日不特定多数の人を相手にしなければならないし
怖いだろうなと思います。
この前スーパーで並んで居た時に店員さんに向かって
心無い言葉を浴びせている人を見かけました。
自分が欲しい物が売り切れていたみたいで・・・(-_-;)
みんなコロナ疲れでイライラしているのかも知れませんが
店員さんだって出来れば休んで人と接したくないだろうに頑張って働いてるんです!!有る意味『命がけ』ですよ!!
ほんっと~に腹立たしくて跳び蹴りしてやろうかと思った程です!<(`^´)>
気持ちに余裕が無くなっているのでしょうけど
人対して思いやりを持てない人間は、
周りの人もその人には優しくしないだろうと思います。
人に優しくしろとは言いませんが、
せめて他人に迷惑を掛けないようしていきたいものですね^^;
・・・職種によってそれぞれの悩みは違うけれど
いまはこのウィルスがこれ以上広がらないように個々が危機感を持ち
節度のある行動をとるしか方法がありません。
暫くの間自粛制限が続くでしょうが、なんとか踏ん張ってみんなでこの危機を乗り越えて行きましょう!
では今日はこの辺で!
投稿: 2020/04/12
本年も宜しくお願い致しますm(__)m
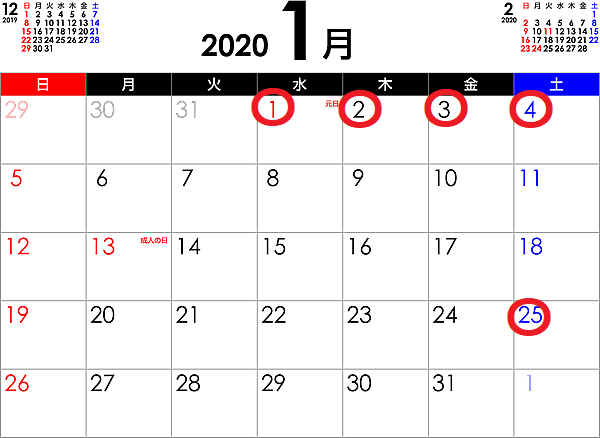
新年明けましておめでとうございますm(__)m
昨年後半はドタバタしており、気が付いたら新年を迎えていたという感じです(^^;)
そんな中、弊社をごひいき頂き支えて頂いたお客様、
色々と助けて頂いた協力会社様に
心より感謝及び御礼申し上げますm(__)m
なかなかHPを更新する時間もなく今日に至ってしまいました(^^;)
取り急ぎ1月の休業日のお知らせです。
(赤い日はお休みです)
昨年は半ばでの社長交代も相まり、
弊社にとっては怒涛の一年で有りました(*_*;
新体制になり、新しいお客様とのお取引も増え、
今までになかったような仕事もこなすようになり
今までの体制では厳しい局面ともぶち当たり、
今後の弊社への課題も浮き彫りとなり
体制改革や人員増強等も含め、今年は更なる飛躍を掛けて
様々な事を改革していかなければならないと痛感いたしました(;´・ω・)
正直、製造業に携わる者の端くれとして
嫌な報告も数々受けた一年でも有りました。
協力会社の廃業や知っている会社の倒産...
製造業も淘汰されていく時代になってきたのかと胸が締め付けられる想いです(-_-;)
・・・
近年・・・
色んな業界で淘汰が進んでいると思います。
例えば、ガソリンスタンド...
色んなメーカーが淘汰され(ENEOS)ばかりが目に付くようになりました。
地域にもよるのでしょうが、コンビニにしても(セブンイレブン)ばかりが街中に点在していると感じます。
(当方の住んでいる半径5キロ圏内に6~7軒ほど有ります(^^;))
セブンカードとエネオスカードがあれば生きていけるのではと思うほどです(^^;)(笑)
勿論それを否定する理由もなく、
実際、当方自身もすごく利用させて頂いております。
2枚のカードも常に活用しております('◇')ゞ
ただ、たまにはミニストップのアイスが食べたいな~とか
ファミマのチキンが食べたいな~と思う事もあるので
もっといろんなコンビニがバランス良くあったら良いのにと悩ましい感じもしています(-_-;)
結局利便性を考えると近場のセブンという結論になってしまいます。
でも同じような距離にあるセブンイレブンでも
『行くセブン』と『行かないセブン』が有ります。
売っている物は同じだし、値段も同じです。
・・・
まぁ、車が停めやすかったりなどの理由も有りますが
一番の理由としては『店員さん』です。
店員さんがテキパキしていて親切で感じが良いお店に行きます。
そう感じるお店はやはりいつもお客さんが沢山います。
同じ物を同じ値段で買うのなら気持よく買い物がしたいですよね?
・・・
製造業にも通ずる所があるなぁと感じました。
色々な板金屋がある中で、同じ物を作るとしたら
材料の値段はほぼ同じです。
まあ、持っている機械などで多少は時間が変わってきますが
工程にかかる時間や技術料金などをプラスして見積もりをします。
なので、正規の見積もりをすればどこの板金屋さんでも
そんなに違いは出てこないと思います。
数ある板金屋の中でお客様に選んでもらうには
何かしら『同じ値段ならあそこに頼もう』と思って頂ける努力をしなければなりません。
確かな品質と丁寧な作業は勿論、
ご相談が有ればお客様の立場になって考え真剣に向き合い
コストダウンの為の提案などにも今まで以上に力を入れていきたいと思います。
後はやはり『人』なのだと。
当たり前の事ではありますが、電話応対や取り次ぎなども含め迅速で丁寧に行い、
お客様に失礼のないよう、気持ちよくお取引していただけるよう、従業員全員で徹底していかなければと感じております。
今や『速い!』『安い!』『上手い!』は
製造業に当たり前の様に突きつけられる条件の様な気がします。
そんな中でも『求められている事+1』を
試行錯誤しながらも実現していける会社で有れればと思います。
製造業に求められる事って何だろう?・・・
『自分だったらこうしてほしい』をコンセプトに
今年は今まで以上にアンテナを張り巡らせていこうと思う所存で有ります!!
ですが
どうしても避けられない課題も多くあります。
ステンレスの材料の値上げ。
レーザーで金属を切断する為に使用する
『窒素」や『酸素』の大幅な値上げも告知されており
この波をどう乗り切るか、協力会社、及びお取引先へ
丁寧に説明し御理解、ご協力を求めていかなければと思っております。
・・・
その反面、近年『コストダウン』を求められる局面も多く
弊社内の工程の見直しや材料取りも含め
協力できることは精一杯協力させて頂く所存です。
しかしながら、どれだけ頑張っても
ご要望に添えない物に関しては
『無理な物は無理』と断る勇気も必要なのかなと思います。
弊社が生き残っていく事がお客様への利益に繋がると信じ
今年も精一杯頑張っていこうと思っております!
本年も木附製作所をどうぞ宜しくお願い致します!!
投稿: 2020/01/01
新旧交代🚗
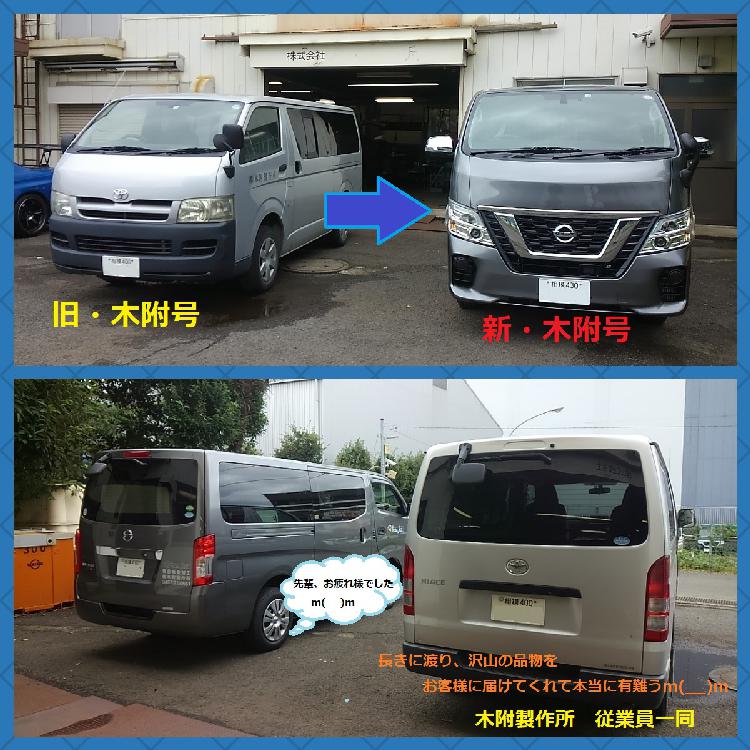
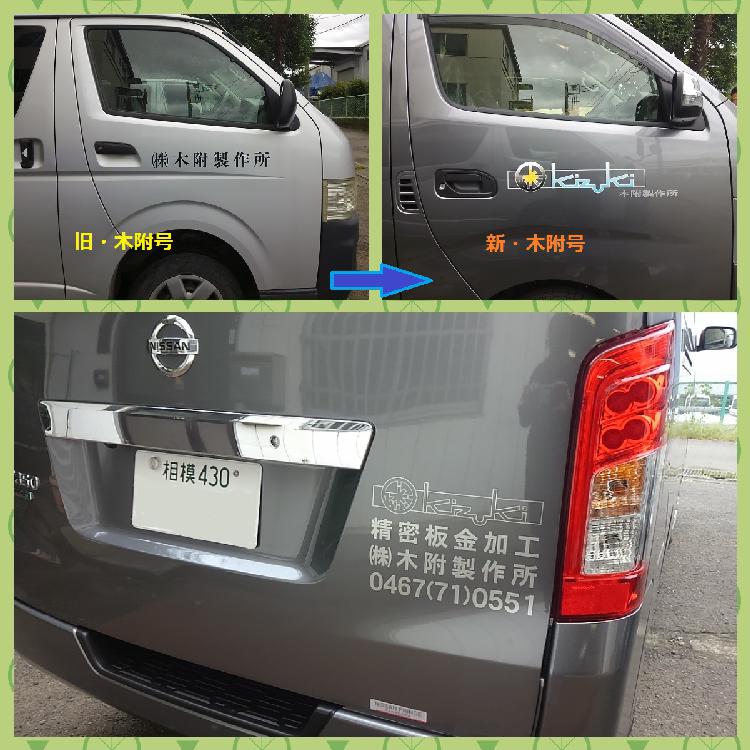
え~、
本日は日曜日でしたが諸々の所用がありまして出勤しておりました。
まず、当方の中で本日の最重要課題として
社用車(納品車両)の入れ替えへの立ち合いです。
・・・
旧車両、(シルバーのハイエース)から新車両、(ガンメタのキャラバン)への新旧交代を本日行いました。
旧車両...
見た目はまだまだイケる感じだったのですが
もう十数年以上頑張っていて、走行距離もウン十万㌔に達し
いたる所にガタがきていて、走行時の振動も大きくなってきてしまい
このままでは納品する品物への傷等などの心配も否めないという事で、
断腸の思いでお別れをする事を決断しました(T_T)/~~~
・・・
当方が入社した時にはもうあったのですが
その頃はピカピカの新車で、入社当初、外回りをしていた当方は
この車に乗って雨の日も風の日も色々な所に納品に行きました。
トラブルがあって納品先で怒られて泣きながらハンドルを握って帰った事も有りました。
急ぎの品を高速を飛ばして届けて『本当に有難う‼』と感謝して頂き
帰り道、嬉しくて鼻歌を歌いながら運転する事も有りました。
・・・
数年が経ち、現場や展開の仕事が主になり
あまり乗る機会は無くなってしまったのですが
お昼休みにお弁当を買いにコンビニまで走ったり
外をまわれる人が出払っているときにピンチピッターで出かけたり
会社で怪我をした仲間を病院に乗せていったり
『トイレットペーパーが無い!』と言われてはホームセンターに走ったりと...
あぁぁぁ・・・( ノД`)・・・・
ダメだ(ノД`)・゜・。
色々思いだしたら、もう泣けてきて(ToT)・・・
・・・
明日・・・
顔が土偶みたいになってるかも(ϴωϴ:)(汗)
本日、旧車両を見送るときも、もう本当に感謝の気持ちが沸き上がってきて泣けてしまいました。
本当に、長い間有難う。
そしてお疲れさまでしたm(__)m
・・・なんか私情の話になってしまって申し訳ありません(;´Д`)
・・・
当方、機械とかへの思い入れが強い方で
数年前にレーザーを入れ替える時も号泣でした(/_;)
機械や車を動かすのは人間なのですが
機械や車が無かったらどうにもならないし
今まで頑張ってくれた事に感謝の気持ちしか無いです。
新しい機械や車は性能や見た目も良いですが
それを導入する事が出来たのは
もちろん、お客様が弊社を支持し続けて下さった事が第一ですが
会社や従業員の頑張りもしかり、歴代の機械や車があっての事だと思っています。
これからも奢らず、色々な事や色々な物に感謝する気持ちを忘れずに
真摯に仕事に取り組んでいきたいと初心に帰った一日でした(*‘ω‘ *)
では、今日はこの辺で(ϴωϴ)ノ←土偶確定。
投稿: 2019/10/20
10月の休業日のお知らせと消費税💰
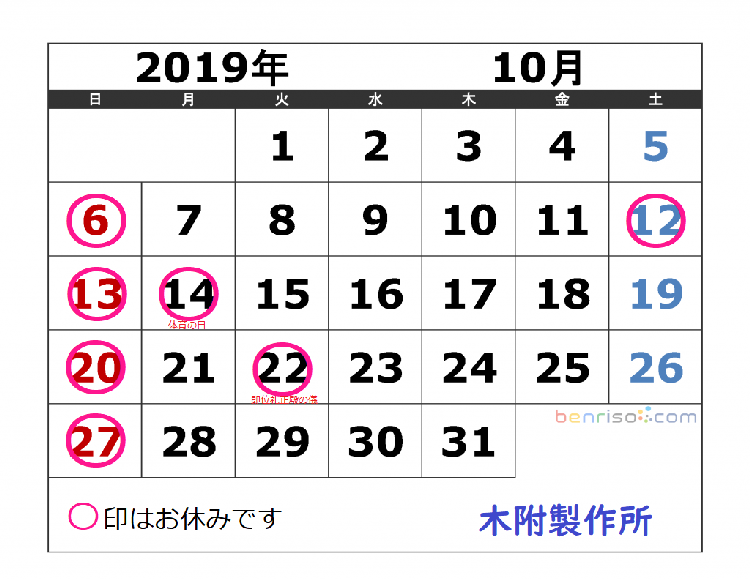
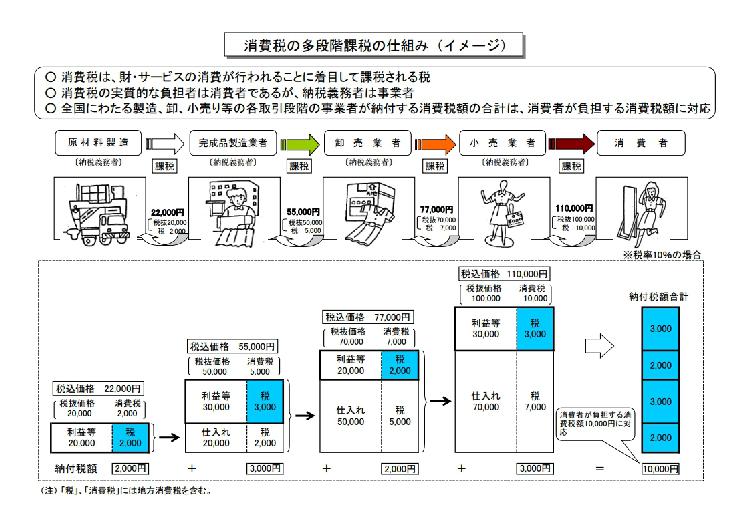
少し遅れましたが10月の休業日のお知らせです(*_*;
ここのところ、ちょっと仕事が立て込んでおりまして
HPの更新もなかなか出来ずに今日に至ってしまいました(^^;)
まぁ、暇でやる事が無いよりは全然良いのですが(^^;)
珍しく休日を自宅で送ったのですが
『家の事もあれもこれもやらなくては』と
思う心とは裏腹に体と脳ミソがそれを拒絶し
ダラダラと一日を終えてしまいました(*_*;
休みたい一心で図面を持ち帰って来たのですが
手付かずの状態で、そのまま会社に持ち帰ります(^^;)←ダメな奴
さて話は変わりますが10月に入り『消費税が10%』に上がりましたね(;´・ω・)
当方…あまり経理の方には踏み込んでいないので
社内のシステムをどう移行したかもよく解っていないのですが
一般庶民として『ん?』と思う謎が有ります。
2枚目の画像は『消費税に関する基本的な資料』と題された
財務省のHPから抜粋したものです。
要は、単純に2%上がっただけみたいな感覚でしたが
よくよく考えると、その2%が何重にも加算されている事になり
結果として最終ユーザーに届く時には実際には今まで以上の負担がかかっているんだろうな~と思いました。
『食品は8%のまま据え置き』というのは一見体裁の良い聞こえですが、
今日、久々に買い物に出かけて
『全般的に食品や飲料の値段が根本的に上がっている(; ・`д・´)!』
と感じました。
・・・
よくよく考えれば『そりゃそうだよな』とわかる話です。
なぜなら、食品メーカーがそれを作るための材料の調達には課税があるだろうし、
パッケージングや梱包したりする資材の税金も上がっているだろうし
その後もメーカー→問屋→小売り→エンドユーザーの届く間にも
税金がどんどん加算されていくだろうし
その合間合間に入っている輸送業者の運賃に対しても税金が加算されているんだろうな・・・
と思って眠れなくなってしまいました(◎_◎;)
一体、最終ユーザーが食品を手にする時にどれだけの税金が上乗せされているんだろ(;´・ω・)・・・
・・・そう考えると弊社の製品もおんなじことなのかな・・と
鉄板を作る製鉄屋さん→鉄板卸問屋→鉄板小売業者→そこから品物を造る弊社→
(弊社だけでは加工出来ない場合は協力会社(2次加工など))→弊社に注文をしてくれたお客様→エンドユーザー
・・・『→』の数だけ税金が加算されているんだろうな・・・(;´・ω・)
・・・
それに反比例するかのようにコストダウンが求められる事も多く
これから、その課題にどう対応していかなければならないのか
先送りに出来ない問題が浮き彫りになってきました。
・・・
もはや企業努力やVA提案ではどうにもならないところできているような・・・
適正な値段で製品を送りだしたいのですが
今までの価格でやっていると
実際は『材料代』にしかならないなんて物も出てきてます。
・・・
しかし実際問題、なかなかお得意様に値上げを要求するのも気が引けるし、
お願いしたからと言って受け入れてくれるとは限らないし悩みどころです(;´・ω・)。
お客様の利益をサポートさせていただくのは
弊社の使命と考えておりますが、弊社が生き残って行く為にも
今後、なんらかの策を考えなければいけない時期が来たのかな・・・
なんて、考えてます。
他の中小零細の製造業の皆様はどう対処しているんだろ(;´・ω・)?←井の中の蛙大海を知らず
・・・
地域の色な々会社の方達と意見交換や情報の共有をして
今後も活躍していけるような体制を作らなければ!と思っています。
それに先駆けて、8月に神奈川産業振興センターに会員登録もしました。
いろいろな中小零細の会社を支援したりセミナーを開いたりしているのでなにか参考になればなと(*‘ω‘ *)
・・・
今までどうりやっているという安定感もしかり、
今までやっていなかった新しい取り組みも大事だと思い
新体制のもと、日々挑戦を続けているところです。
9月19日に開かれた神奈川産業振興センター主催の商談会にも
初めて参加してみました(*‘ω‘ *)
その日の事はまた後日、このブログにてお話したいと思います。
・・・気が付いたらもう三時をまわっていたので
今日はこの辺で(^^;)←寝坊の予感
投稿: 2019/10/07
9月の休業日のお知らせとメカトロラーメン🍜
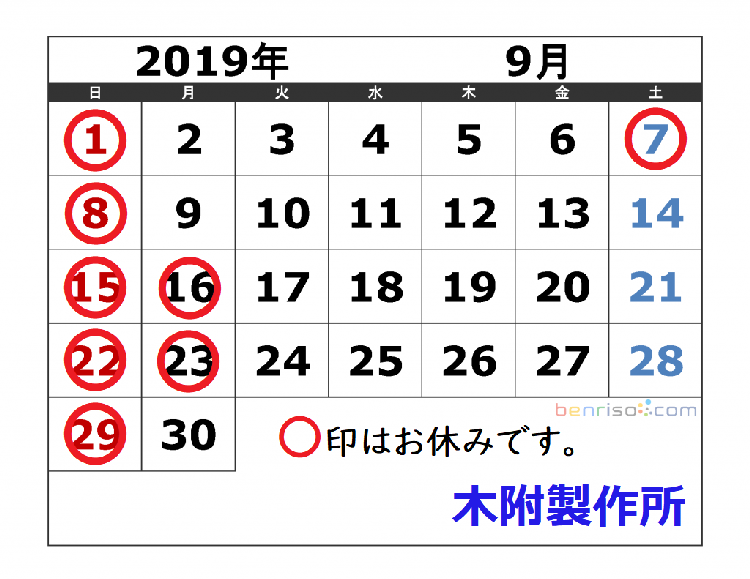
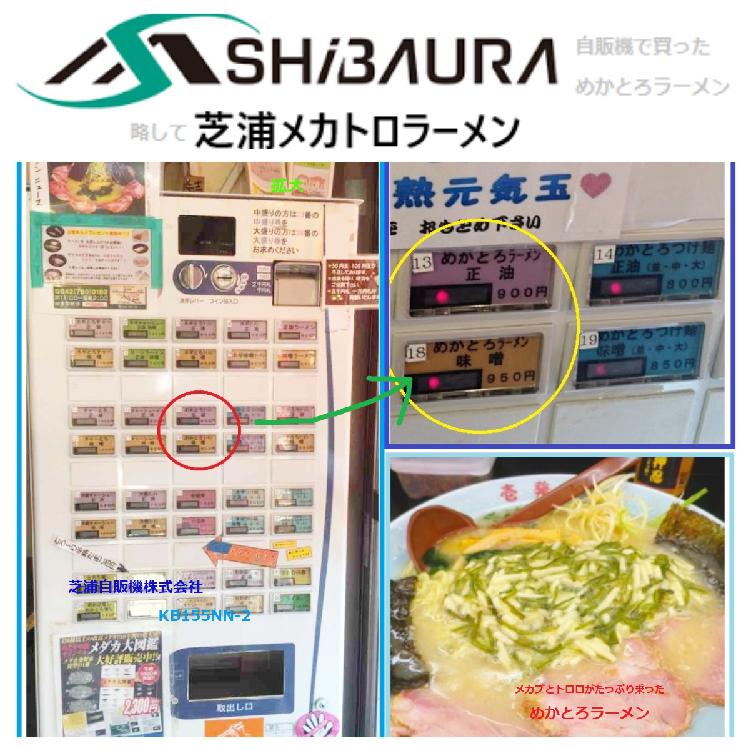
さて、9月に入り今年も残すところ、あと4か月になりました。
もう1年の3分の2を終えた事になりますね(*‘ω‘ *)
『終り良ければすべて良し!』となれるよう
残り4か月、ラストスパート全力疾走で頑張りまっす( `ー´)ノ
・・・
本日は日曜日ですが、ちょっと仕事が立て込んでいまして出勤しておりました(*‘ω‘ *)
新体制になり、少しづつ色々な変化が出てきて
大変有難い事に、新しいお客様とも御付き合いさせて頂く機会も増えてまいりました。
それで今までとは、ちょっと違う感じの品物を製作したりする事も多くなり
今まで
『ここの箇所をこう展開するのは当たり前(*´з`)』とか
『ここはこう処理しした方が良いに違いない('ω')』と
思っていた事が、お客様によっては違っていたりする事も出てきて
個々のお客様の御要望に応えるべく、日々試行錯誤しながら勉強しなおしています(^^;
・・・
話は全く変わりますが
2枚目の写真の説明を・・・(;'∀')・・・
解る人しか解らない話なのですが少しお付き合い下さい(^^;
弊社が日頃大変お世話になっているお客様に
【芝浦メカトロニクスグループ】様がいらっしゃいます。
芝浦メカトロニクスグループって何をしている会社?
…
テレビや冷蔵庫とといった
一般家庭には、直接なじみのある品物を提供している訳では無く
ピンとくる人も少ないのではと思いますので簡単に説明を(*'▽')
※FPD製造装置、半導体製造装置、真空応用装置、YAGレーザ装置、マイクロ波装置、
鉄道保線保守機器の製造、券売機・チャージ機・自動販売機の開発販売、保守、開発や設計販売など
様々な分野を各グループで展開しており
海外でも拠点を持ち世界でも活躍している会社です。
※FPDとはフラットパネルディスプレイの事で、ブラウン管に代わる薄型で平坦な画面の薄型映像表示装置の総称です。
FPDには、液晶ディスプレイ、プラズマディスプレイ、有機ELディスプレイ、FED(フィールド・エミッション・ディスプレイ)、電子ペーパなどがあります。
...
わかりやすく漠然とザックリ説明するとしたら・・・
テレビやスマホの画面やそれを動かす半導体…
それを作る為の装置を作ったりしているといった感じです。
今手にしているスマホや、自宅にあるテレビ…
表立ったメーカーの名前は違うかもしてませんが
芝浦さんや、そのお手伝いをさせて頂いている、
弊社が関わった品物かもしれませんよ~(*'▽')
前置きが長くなりましたが、写真は当方がかれこれ十数年通っているラーメン屋さんの発券機です。
芝浦メカトロニクスグループの芝浦自販機株式会社が
2004年頃~2006年頃に販売していたKB155NN5-2というモデルでは無いかと思われます。
(ちなみに、もう一軒通っているラーメン屋さんがあるのですが、そこも芝浦自販機の発券機です(^^))
現在の最新モデルは液晶ディスプレイのタッチパネルの物もあったりと、だいぶ進化していて高速のSAなどで見かけたりします(*‘∀‘)
..で、
なにが言いたいのかと言うと...
『メカトロラーメン』....って…(^^;)…
と、最初にメニューを見付けたときは冗談かと思いました(^^;)
・・・
メカトロラーメン、、、
想像では麺が配線コードかなんかでナルトが歯車(◎_◎;)??
背油の代わりに機械油(; ・`д・´)?
いやいやそうではなく、なんと『メカブ』と『とろろ』がたっぷりトッピングされたラーメンなのでありました(^^;)
・・・。
芝浦自販機の発券機で売っているメカトロラーメン・・・
当方の中ではもう10年以上『芝浦メカトロラーメン🍜』と認識されています(^^;)
正直言って・・・
一回も食べた事は有りません(^^;)
・・・なんか
恐れ多くて・・・(^^;)(汗)
しかし食べたことのある友人に聞いたところ
こってり系のラーメンにさっぱりとしたメカブとトロロは
以外にも相性が良く美味しいらしいですよ(*'ω'*)
『食べてみたい!!!』と思った方はご連絡頂ければ
お店を紹介させていただきますよ(^O^)/
では今日はこの辺で(=゚ω゚)ノ
【※前回のブログに書いた、当方宅で保護していた珍客さんは翌日に飼い主さんが見つかりました!
一緒に過ごしたのは、たった一日だけでしたが、いなくなると少し寂しい気持ちになりました(._.)・・・
でも、元気な状態で無事にお返しすることが出来て良かったです(*‘ω‘ *)】
投稿: 2019/09/01
8月の休業日のお知らせと珍客さん
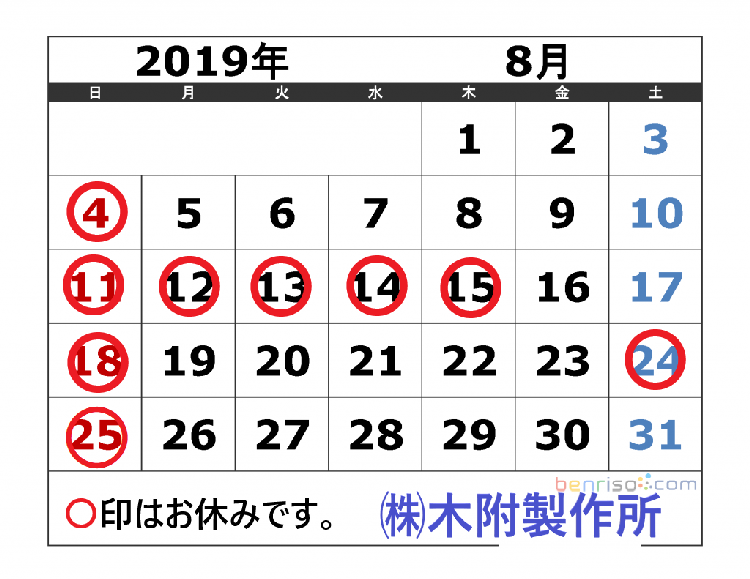
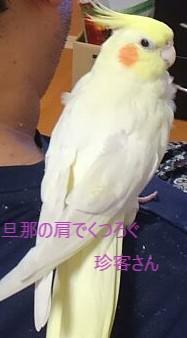
本日よりお盆休みを頂いております。
・・・あ!
しかしお得意様の中で緊急の案件がありましたら
弊社社長にご連絡頂ければ対応致します(=゚ω゚)ノ←勝手に判断してる奴
とりあえず『このお盆はどこにも行かない( 一一)』という
従業員が何人かいるので招集かければなんとかなると思うんで(*‘∀‘)
・・・と言う当方も今の所、どこにも行かない予定ですが('◇')ゞ(笑)
一日位は実家に帰ろうかな~と悩んでいるのですが
なんせ暑くて屋外に出る気になれません(;´Д`)←ダメな奴
・・・それに
本日の夕方、買い物に行こうと玄関を出たら
玄関脇の植え込みから『ガサガサガサッ!』と不穏な音がっ!!!
『ひぃぃ━Σ(゚Д゚||)━っ』と奇声を上げながらも
勇気を出して音のする方を覗き込んで見ると
なんと、どこからか逃げ出してきたオカメインコが飛べずに右往左往しているのでありました🐦
当方の住んでいる所は野良猫さんも多いので
ほっておく訳にもいかないし、とりあえず珍客さんを屋内に招き入れる事にしました。
近所の物知りおじさんに心当たりは無いか聞いたのですが
わからないようで・・・(;´・ω・)コマッタ・・・
とりあえず間に合わせで餌と菜っ葉を買ってきて
少しは食べてくれたので一安心(*'▽')
少したったら部屋の中を飛び回るようになったので
骨折とかはしていないみたいで良かったです(*‘ω‘ *)
しかし珍客さんを置き去りにして家を空ける事も出来ないし
明日から飼い主さんを探さなくては(;´・ω・)・・・
ではでは珍客さんもやっと眠ったようなので
当方もそろそろ寝ます(p_-)ZZZ
みなさんもお体に気をつけて夏休みを楽しんで下さい!
ではまた(=゚ω゚)ノ
投稿: 2019/08/11
MF-TOKYO 2019へ行ってきましたっ(≧▽≦)ノ
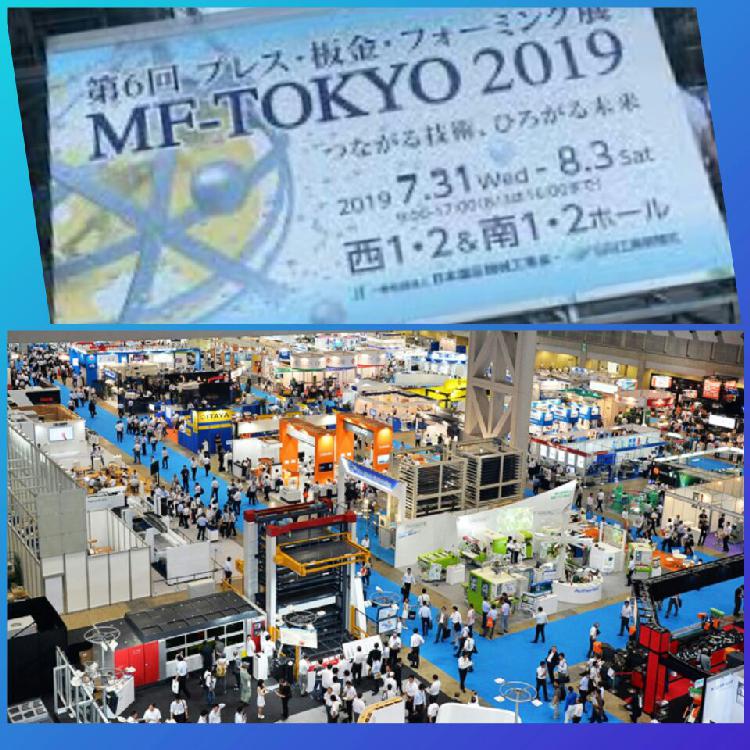
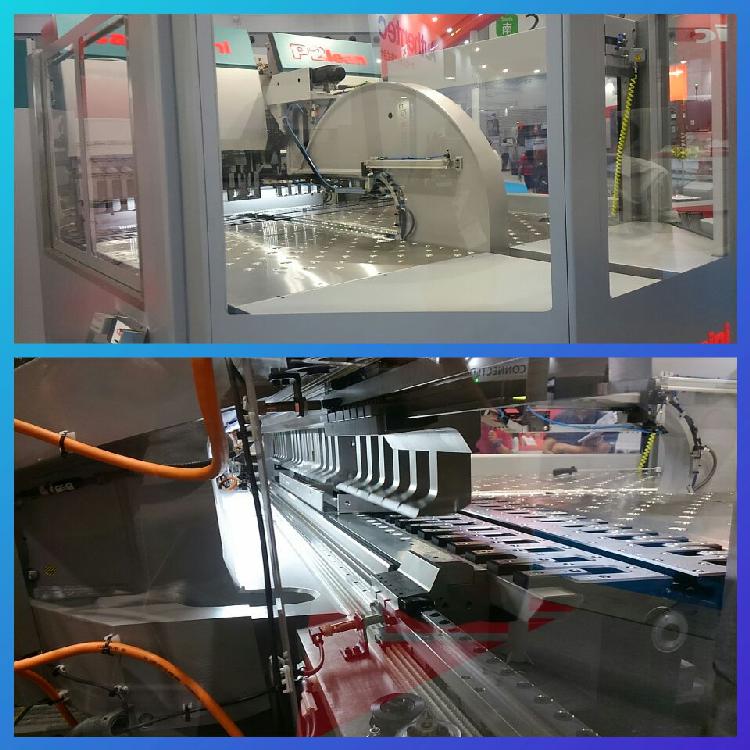
8月3日(土)
7月31日(水) 〜 8月3日(土)に東京ビックサイトで開催された
第6回プレス・板金・フォーミング展
MF-TOKYO 2019へ弊社社長と2人で行って参りました( `ー´)ノ
『MF-TOKYO』って何?
と思われる方もいらっしゃるかと思うので簡単に説明を('ω')
2009年から2年毎に開催されている国内最大の鍛圧機械(=プレス機械や板金機械など)の専門見本市で、今年で6回目を迎えます。
各種プレス機械、レーザー加工機、プラズマ加工機を含む板金機械、フォーミング機械などに加え、
周辺産業の出展も増えて有力メーカーが一堂に集結する、板金屋にとっては、あれもこれもと
無限に欲しいものが溢れている夢のような空間が広がる祭典で有ります(≧▽≦)!
平日はお得意様が営業されておりますので
何か緊急の案件が入ったら対応しなくてはいけません。
なので逸る気持ちを抑えて最終日の土曜日に行く事にしたのですが
『さぁ!行くぞ』と意気込んで家を出たものの
高速入り口付近で会社からの緊急入電(◎_◎;)
土曜日も営業しているお客様から緊急の依頼があり一旦会社へ。
いつもお世話になっているお得意様が困っているのに見て見ぬふりは出来ません(>_<)
急いで会社に向かい、レーザーを立ち上げ依頼の品を制作し
無事に引き渡す事が出来ました。
お客様に『有難う!助かった!』とのお言葉を頂き
『やって良かった!』とうれしい気持ちになりました(^-^)
さてさてしかし時は刻一刻と過ぎていきます。
急ぎ再度ビックサイトへ向かいます( `ー´)ノ
・・・しかし途中、首都高の渋滞にはまり
会場付近に着いたのは午後2時位。
そして新たな試練が・・・(; ・`д・´)
なんと、周辺駐車場はほぼ満車(;'∀')・・・
会場から少し離れてはいたけれど『空き』のある駐車場を見つけ
車を停め急いで向かいます。
やっと会場に入ったのは午後2時半を回っておりました。
だけど5時までやってるはずだから『まだ2時間半は見れる!』
取り急ぎ、絶対見たかった機械を置いているメーカーへダ~ッシュ!!ε=ε=┏(;≧д≦)┛
と、思っていたのですが、そこまでたどり着く間に
各メーカーのブースに魅力的な機械達が置いてあり実演加工のデモをしていて
ちょいちょい寄り道をしては心を奪われて動けなくなり、
しまいには社長とはぐれてしまうという大失態(-_-;){ゴメンナサイ
しかし、『ここで社長を探している時間は無いっ!!残りの時間は出来るだけ色んな機械を見たい(; ・`д・´)!』
と開き直り一人で最新の機械達を見て回っては
『こんなの欲しいな~(*^▽^)』
『これがあれば、あんな事もこんな事も出来るな~( *´艸`)』
と夢を膨らませ妄想が加速していくのでありました(^^;)
途中偶然に社長と再会して自分の気に入った機械を猛アピール!
そのブースに案内して一緒に説明を聞いたりしました。
説明を受けている社長の背後から
『買ってくれ~買ってくれ~( ѡ`Д´)ѡ{★▽◎◆~』と念を送ったのですが
即効性はなかったようです(=_=)
しかし今後実際に導入を検討する機械は3台位見つかりました。
・・・まぁ、欲しいと思う分にはタダですから(^^;)
・・・だって、欲しいと思った機械の値段を聞くと
安くても1000万近くするんです((((^^;)・・・
凄い物になると『億』の世界なんです(((((((((((^^;)・・・
①機械を入れれば今まで以上にやれる事が増えて売り上げがあがる。
②機械を入れるお金を稼ぐ為に今まで以上に頑張って売り上げを上げる。
『鶏と卵どっちが先?』的な考えが頭の中をグルグル回って正解は導き出す事は出来ませんでした。
そんなこんなしてる内に会場に『蛍の光』が!
『えっ⁉もう5時っ(゚Д゚;)⁉』
時計を確認するとまだ4時です。
5時で終わりと思っていたのが大誤算・・・
ガ━━━━━━∑(゚д゚lll)━━━━━━ン !!
なんと最終日は午後4時までだったのであります・・_| ̄|○ ガクッ
・・・『まだまだ見たいブースがあったのに・・・ 』
と後ろ髪を引かれる思いで会場を後にしたのでした・・・(lll-ω-)ズーン
・・・
最新鋭の機械を導入する為にはお金が沢山かかります。
でもお金を掛けた以上に効率が上がり仕事の幅が広がって
利益も上がるのかもしれません。
これから先、どうするのが弊社やお客様に一番プラスになるのかを
会社のみんなと話し合い、考えて、色々な取り組みに挑戦していきたいと思います!
....
今や製造業全体が人手不足で高齢化も進んでおります。
機械に頼ざるを得ない問題も沢山出てきているのも確かです。
その反面、機械が人間の仕事を奪い、失業率も上がっていくのではとの懸念も有ります。
難しい問題ではありますが、機械や技術の進歩と
人の感性でしか作りえない物とを融合してもっともっとより良い
物造りをしていけたらなと思います。
商売をしてる以上、自らの利益を追求することは必然ですが
弊社に関わっている協力会社の皆様や、お得意様、そして弊社の品物を最後に手にするエンドユーザー。
みんなが笑顔になれるような物造りを続けていけたら
最高に幸せだな~と思いながらこのブログを書いています(*‘ω‘ *)
半導体の低迷、アメリカと中国の確執、日韓問題・・・
まだまだ日本の製造業にとって不安要素は山積みではありますが
この波を乗り切った暁には明るい未来が待っているに違いない( `ー´)ノ←楽観的な奴
日本の中小零細、製造業の皆様!
力を合わせて頑張っていきましょう( `ー´)ノ!!
では本日はこの辺で(=゚ω゚)ノ
投稿: 2019/08/07
代表取締役社長交代のお知らせ
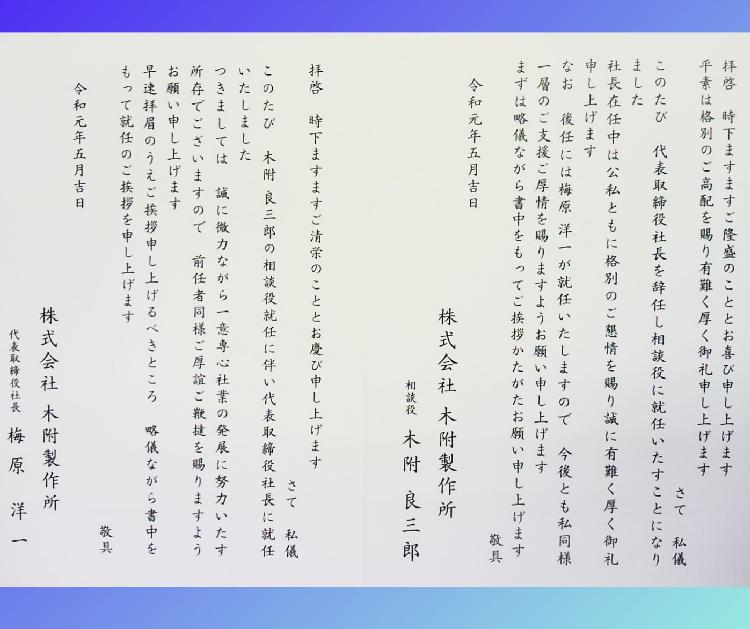
遅ればせながら御報告させて頂きます。
弊社先代社長、木附良三郎の相談役就任に伴い
前工場長の梅原洋一が代表取締役社長に就任致しました。
新体制のもと、従業員一丸となり
今後ともお客様のご期待にお応え出来ますよう、
今以上に、より良い製品作りに努めてまいります。
今後とも木附製作所に変わらぬご支援を
どうぞよろしくお願い致します。
~株式会社 木附製作所 従業員一同~
投稿: 2019/07/26
色んなリニューアル
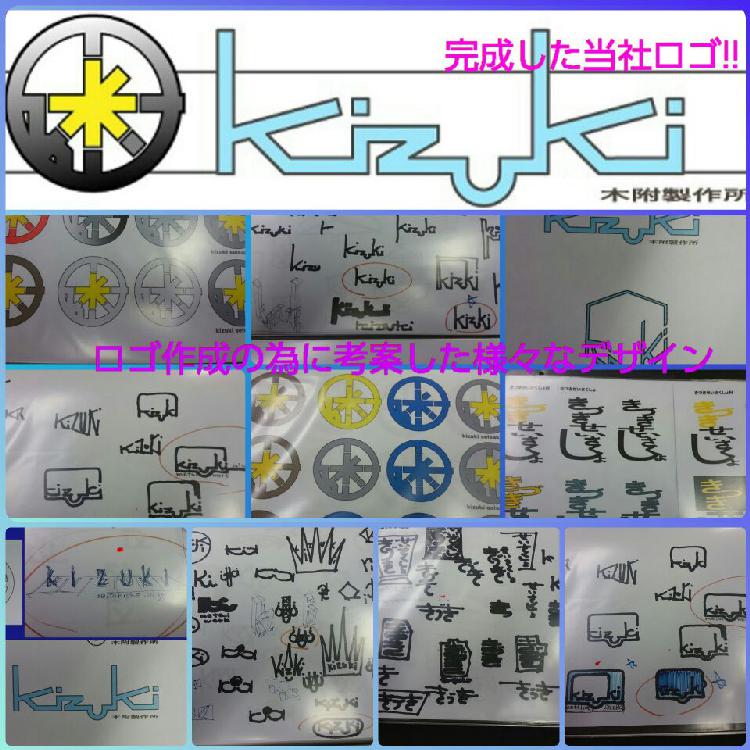
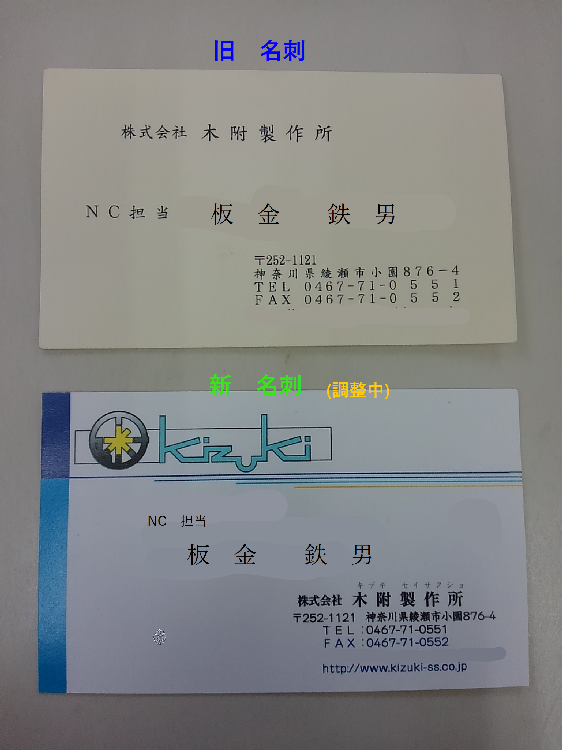
ホームページが正式にリニューアルオープン致しました(^o^)丿♪
ホームペー公開に伴い当社の『ロゴ』もリニューアル!
(トップバナー参照(^^))
そしてこのロゴを使って『名刺』もリニューアル!
(写真はクリックで拡大できます!)
ちなみに初対面の方などに『木附製作所』ってなんて読むの?
と言われたりします・・・^^;
当方も入社前は『なんて読むんだろう^^;・・・』
『きふ?製作所』『もくふ?』なんて思ってました^^;
正式社名は『キヅキセイサクショ』と言います。
そこで誰が見てもわかるように『ロゴ』をローマ字にしました(^_^)
名刺にはフリガナも入れました(*'▽')
デザインはブログ内でチョイチョイ出てくる検査主任のS氏です。
元々芸術系の大学を出ているのでこういう事は殆どS氏に丸投げします((笑))
当方は、このロゴを元に新たな看板製作を模索中です(゜゜)
さて、リニューアルとは少し意味が違うかも知れませんが
もうすぐ『年号』も平成から令和に変わりますよね?
そう!!
今日は平成最後の日!!
明日には令和になっているんです(゜-゜)・・・
・・・まぁ、だからと言って
何かが劇的に変わるという事も無いんですが^^;
でも、この節目を機会に
『色々と新しい取り組みにも挑戦していきたいな』
なんて思ったりしています。
・・・ちなみに
この前、会社の古い書類を整理していたら
すっごい昔の『履歴書』のファイルが出てきて
『知らない人ばっかりだなぁ・・・』とパラパラめくっていくと
生年月日の欄に『大正』と記載された諸先輩方が
何人か見受けられました(@_@;)ビックリ!
当方も当方の親も昭和生まれなので
あまり『大正』という年号に免疫がなく驚いてしまいました^^;
それと同時に
この会社が長年にわたり築いて来た
歴史と信頼の重みをひしひしと感じました。
そして、代々の諸先輩方から
知識や技術を受け継いできたように
自分達もまた、後に続く者として
良いものを残していかなければと
背筋が伸びる思いがしました。
・・・
何十年か後に
未来の後輩が当方達の履歴書を見つけて
『昭和かよっΣ(@Д@;)!!』
と驚いて、当方と同じような気持ちになってくれると嬉しいなぁ(^-^*)←妄想中
・・・その為にはまだまだ精進して頑張らねば(゜へ゜)
【オマケ】
★今日の板金屋標語★
『良いものを 残していきたい 後世に 『温故知新』の 精神で!』
…
本日は平成の締めくくりという事で
真面目に考えました(^-^)
『温故知新』…
当方の好きな言葉の一つでして('ω'*)←(実はコトワザと四字熟語マニア)
古代中国の思想家である「孔子」の言葉と言われています。
原文は「子曰、温故而知新、可以為師矣」となっており
四字熟語やことわざとして「温故知新」の部分だけが伝わったものと思われます。
読み下しとしては
「故を温ずねて新しきを知る」
古きをたずねて(あたためて)新しきを知る。
意味としては『温故知新』の部分だけ切り取ると
『古くからの教えや、前に学んだ事をもう一度調べたり、考えたりして新たな知識を見いだし、自分の物にする事』
なのですが、その後の言葉も含めて全体的に解釈すると
『古くからの教えや、前に学んだ事をもう一度調べたり、考えたりして新たな知識を見いだす事が出来れば、人を教える師となることが出来る』
といった感じです。
仕事は勿論、私生活においても行き詰まったり悩んだりした時
昔のことを知って学んだり、誰かから経験談を聞いたりして
ふと解決したりすることがあります。
技術や環境はどんどん新しくなっていくものですが、
これまで蓄積してきた経験や知識をおろそかにせず
それに新しいものを加味してもっと良いものが手に入ると良いですね!
日本の製造業はまさに
その精神でここまで成長してきたのではないかと思います。
『平成』は戦争の無い平和な時代ではありましたが
経済的には未曾有の不況の時代でもありました。
『山一証券倒産』や『リーマンショック』…
その中を歯を食いしばって共に踏ん張った
中小、零細の製造業の皆様。
明日から『令和』という
新しい時代が始まりますが
この節目が自分たちにとっても
皆様にとっても良い時代になるといいですね‼
まだまだ色んな苦境にたたされる事も有るでしょうが
地域の中小企業が連携し、お互いの得意分野を持ち寄り
新しいものを生み出したり、大手に負けない体力作りが出来たらいいのにな~なんて思ってます。
…あ、
ただ思ってるだけで、
まだどうしたらうまくいくのか
模索中ですが(^^;←いつも考案するだけで具体案が無い人
もし、これを見ていて
共感してくれて名案があれば連絡下さい(^^;←他力本願な奴
では、今日はこの辺で‼
投稿: 2019/04/30
ウェルドナット(溶接ナット)取付作業
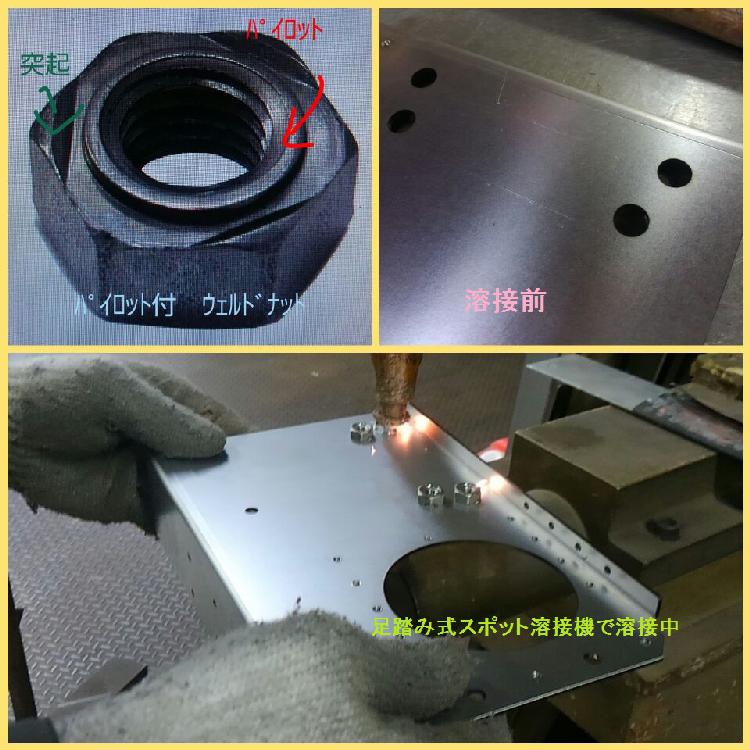
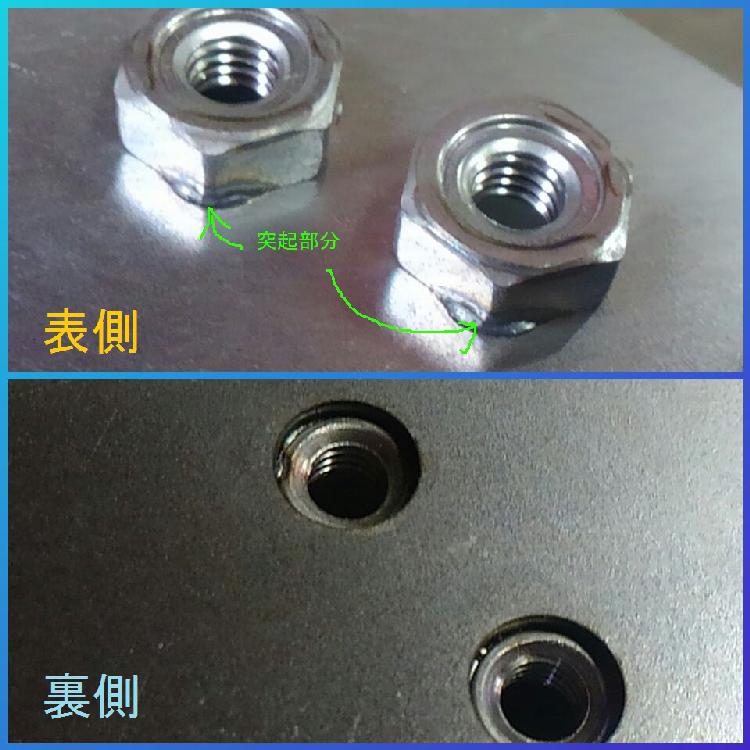
本日は『ウェルドナット』溶接の作業を紹介いたします(*'ω'*)
『ウェルドナット』って何?
と思われる方の為に簡単な説明も含めてお話させて頂きます。
ウェルドナットには様々な形状があり
六角型、四角型、T型なども有ります。
当社で使用しているウェルドナットは
主に『六角型』になります。
六角型の場合は
3方向に飛び出した『突起』(最初の写真の図示参照)を
母材にスポット溶接をするナットです。
(当社では足踏み式スポット溶接機を使っています)
図示の『パイロット』の部分をガイドにして
母材の下穴に合わせます。
溶接したい母材とウェルドナットの上下から電極を当て、
適度な圧力を加えながら電流を流し加熱することで
金属を溶かし、その後冷却する事で
再凝固する働きを利用して2つの金属を接合させます。
俗に言う一般のナットには『ガイド』も『突起』も有りません。
通常のナットを溶接する場合には
ナットの端面と母材の接続面を何か所か
『ナメ付けor肉盛り)』溶接しなければなりません。
この場合、位置決めや溶接に時間がかかります。
相手のある部品の場合『肉盛り』している部分が
何かに干渉してしまう可能性も有ります。
ウェルドと比べて熱をかけている時間も長くなるので
板厚が薄い場合や、ナット溶接個所が多かったりすると
母材が引っ張られて、波打ったり歪んだりしてしまう事も有ります。
2枚目の写真はスポット溶接後の写真になりますが
表側は溶接による盛り上がりも無く、
裏側も焦げが殆ど有りません。
作業性も良く美観にも貢献しているのがおわかりになると思います。
普通のナットと比べたら単価は割高になりますが
量産品でコストダウンが求められている製品に対しては有効だと思います。
しかし、ウェルドは溶接しやすく作業性が高い一方で、
3点での溶接のため安定性は他の溶接ナットに少し劣ります。
点での接合となるウェルドナット溶接は、
線での接合を行うナメ付けや肉盛りの溶接方法に比べて
十分な強度を確保できない場合も有ります。
(かと言ってハンマーで叩いた位では取れません^^)
なので、常に大きな衝撃が加わるような個所に使われる場合や
それなりの強度が求められる様な製品には
ウェルドナットの溶接は行いません。
また、母材の板厚が厚すぎたり、表面処理鋼板の場合
通電しにくいのでこちらもウェルドはあまり使われません。
ナットにはこの他にも色々な種類が有り
母材の材質や板圧により相性が異なります。
例えば『カレイナット』
溶接では歪みやひずみが生じてしまうような薄板や
母材にウェルド以上の美観が求められる様な品物等に
圧入(プレス、押し込み)加工します。
カレイナットの首下部分は独自の形状(ナール・溝部)をしており高い取付強度が得られます。
スチール母材だけでなく、溶接に不向きな母材にも圧入方式でナットを取り付けることができます。
その他にも色々な種類のナットがあり紹介したいのですが
その機会に出くわした時に、また作業工程も含めて
個々の特性等ご紹介出来ればと思います(*'▽')
【オマケ】
★板金屋ジョーク★
(多分同業者しか笑えません(^^;)
☆カレイナット →圧入ナット
☆華麗ナット →ため息が出るような美しいナット✨
☆鰈ナット →右側に2つナットが付いている🐟
(左ヒラメの右カレイ(-_-)サカナカヨ)
☆加齢ナット →くたびれたナット。多分強度も弱い(+_+)
☆カレー納豆 →…もはや板金とは関係無い(;'∀')…
罰ゲームとかで食べるタイプの
ニューテイストカレー(◎□◎♯)⁉
…てか
ホントくだらなくてスイマセン(^^;)
次回はもう少しまともなネタを考えておきます(*´з`)
(そんな暇あったら仕事しろ‼」と怒られそうですが(;'∀'))
では今日はこの辺で‼
投稿: 2019/04/22
丸穴→長穴への追加工
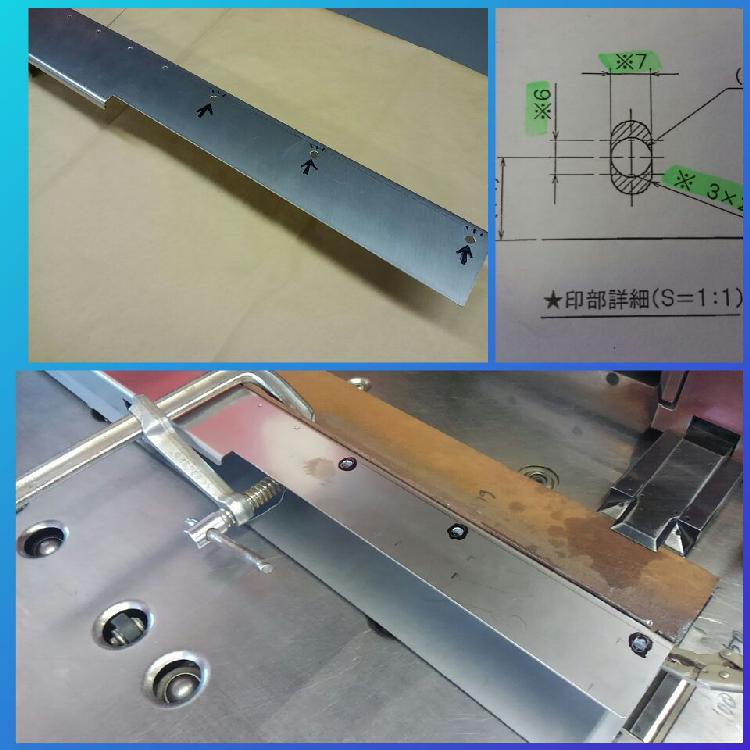
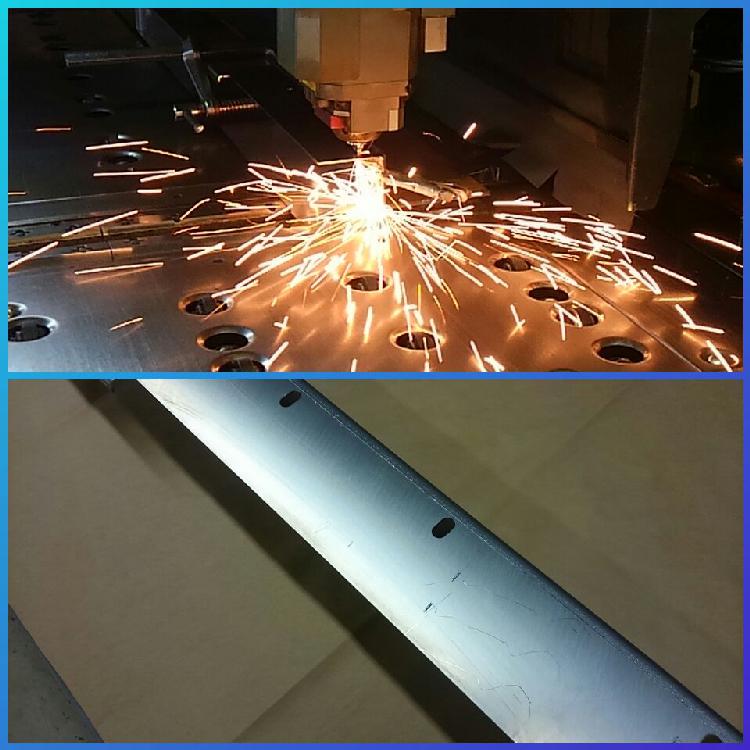
本日は追加工の一例を紹介いたします。
まずは『ツイカコウって何?』と思われる方もいるかもしれませんので
簡単に説明を・・・
完成した製品や既存の購入品に後から更に加工を加える事を『追加工』といいます。
例を挙げると・・・
作っては見たものの、実際に使ってみたら、
組み立時に何かに当たって干渉するとか、穴が小さすぎて入らないとか
なんらかの問題が出た場合に、切り欠きを足したり、
穴を広げたりして不具合を解消するために行ないます。
設計変更で取り付け位置が変わったり
取付部品が多くなったりしたときなどに穴を増やしたりして、
今ある製品を破棄しないでも使えるようにする為に行なったりもします。
最初から作り直すより、価格的にも安く抑えられる事も多く
既存の製品がまだ使えるという事は
ある意味、環境にもお財布にもやさしい加工と言える様な気がします(*^^)b!
・・・時には追加工の内容や、製品の大きさにもより
作り直したほうが早くて安い時もありますが・・・^_^;
前置きが長くなりましたが、
写真は一旦納品されたブラケットの丸穴を
長穴に加工しなおす追加工を行なっているところです。(SUS304 板厚2㎜)
(写真はクリックで拡大できます!)
もう曲がってしまっているので、レーザーやタレパンで普通に掴めません。
セットプレスもこの形状では入りません。
板厚や数量(8個)も考慮し、この品物に合った『※冶具』を作り
固定してレーザーで加工する事にしました。
(※冶具とは→位置決めと同時に加工の案内をする補助工具のことです。
その時の加工に合わせて形や大きさを変えて作ります。
これを使う事で、常に一定の位置で固定できるので
仕上がりが統一されて寸法がが安定します。
数が有る場合は固定・取外しが簡単に出来る構造にしないと
時間が掛かってしまうので、その辺も考えて作ります。)
写真左上から
『元々の穴』→『加工指示の内容』→『冶具に乗せて固定』→『レーザーで加工中』→『長穴出来上がり!』
と言った感じです。
この後、完成品検査にまわし、加工にズレが無いかをチェックして完成です!
この他にも、もっと複雑な追加工などもこなしていますので
『この品物・・・何とかしてまだ使えないかなぁ~』
なんて思ってる物がありましたら気軽にお問い合わせ下さい!
今まで培った経験と技術で最適な提案をさせて頂きます(^^)
『追加工』もぜひ木附製作所へ~(^O^)/
【オマケ】
★板金屋 哀歌★
『鏡見て 「出来ればしたい!」 そう思う。 自分自身に 追加工…(=_=)』
・・・
ある意味、美容整形って人間の追加工みたいなもんなんですかね^_^;?
当方も、昔は
「お金と勇気があったらやってみたいな~」
なんて思う事もありました(-"-;)
・・・
でももうそんな歳でもなくなったので追加工無しで頑張ります!^^;(笑)
では今日はこの辺で!!
投稿: 2019/04/10
5分で設計した『フタ』
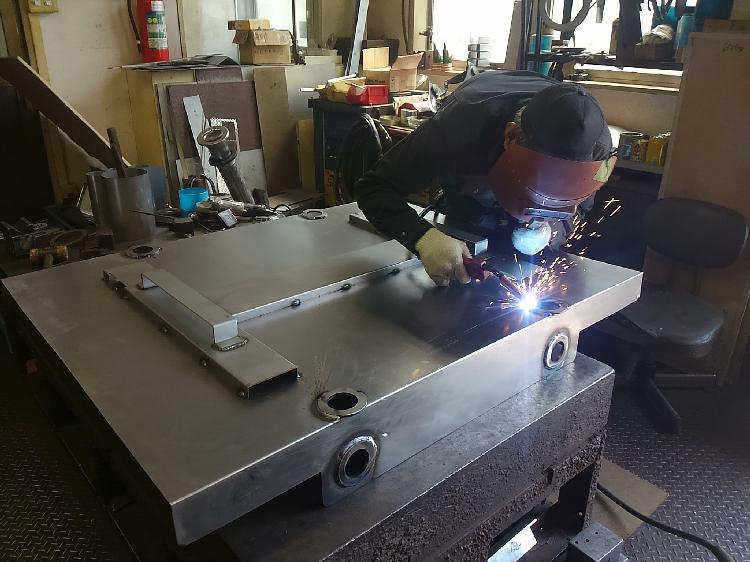
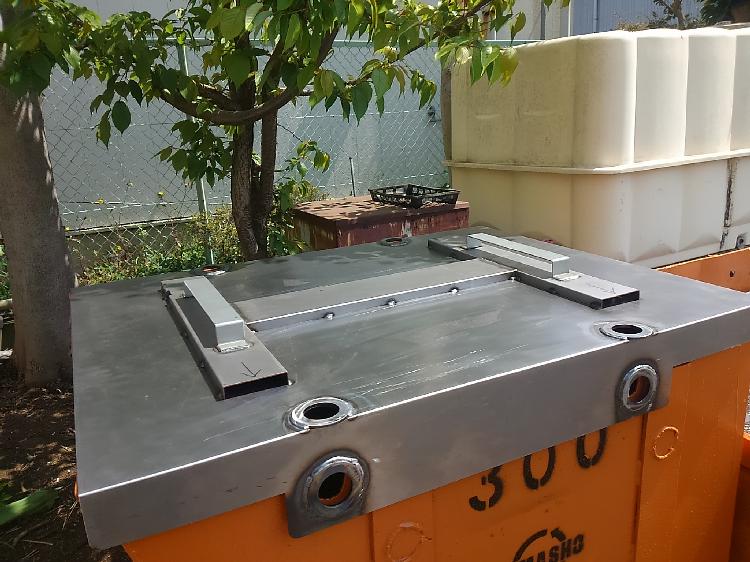
本日も一日現場だったので帰宅後の更新です。
(現場7.5割、展開2.5割です(^^;)
朝、工場長が外に置いてある屑入れ
(加工後に残った廃材をリサイクルにまわす為に貯めておく箱)を
しばらくジィ~~っと見つめていたと思ったら
メジャーで寸法を測り始め、突然何かのスイッチが入ったのかのように
プログラム用紙の裏にポンチ絵(手書きの簡単な図面の様な物)を
書き始めました。
絵が出来上がると間髪入れずにシャーリングでspccの1.6を落とし
レーザーに乗せて、手入力でGコード(どんな穴を何処に開けるかとか、どんな形で外形を切るかとか
切断条件などの指令を出す数字とアルファベットで構成されたコード)を入力し、
切ったかと思ったら今度はベンダーを起動してテキパキと溝と歯をセットし始めました。
こちらも曲げ寸法を手入力し、『バインッ!バインッ!』と
両端をコの字状に曲げ、今度は現場内の屑箱の中から
使えそうな廃材を物色し部品になるであろうものをせっせと作り始めました。
...その間約30分位ですかね(^^;)
曲げ終わったら溶接班のT氏に指示を出し
あれよあれよと屑箱のフタが完成しました。
あ、このままじゃ錆びちゃうからそのうち塗装しないと!・・・
しかし…なんか怒涛の勢いでついて行けなかった(^^;)・・・
てか、頭の中に展開機が入ってるんじゃ・・(^^;)コワイ
で、さっそく出来上がったフタを乗せてみたら
これがピッタリ(◎_◎;)スゴイ‼
即興で作ったとは思えない出来栄えで驚きました(*_*;
みなさんも、『なんかこんなの欲しいな~』と思ったら
うちの工場長に頼むといいですよ(=゚ω゚)ノ
展開、レーザー、タレパン、ベンダー、見積もり等々
一人でこなせるので安く出来るかもしれません(^^;)(笑)
従業員一同、注文お待ちしておりま~す(^O^)/
【オマケ】
★今日の標語★
『リサイクル ちゃんと分別 再利用! 地球に明るい ミライクル!!』
(未来くる‼)
あれっ?
なんか久々にまともな事言ったかも(;'∀')(笑)
ちなみに『鉄』はリサイクルの優等生で
90%を超える鉄スクラップは回収され、
何度でも新しい鉄鋼製品に生まれ変わります。
リサイクル性に優れた鉄スクラップは
循環型社会の構築に貢献しています('ω')ノ!
空き缶だって同じです!
なので皆さん、空き缶はクズかごへ~(^O^)/
では今日はこの辺で!!
投稿: 2019/04/06
会社自慢( `ー´)ノ 【個人的な主観ではあります(^^;】
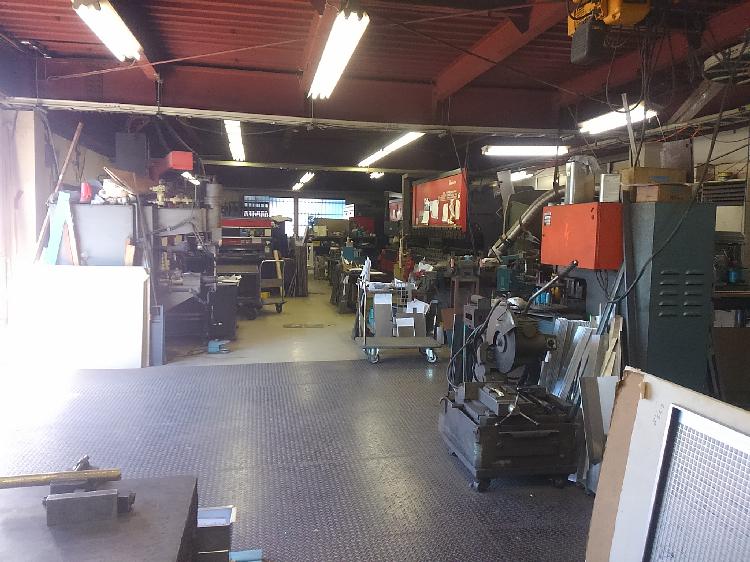
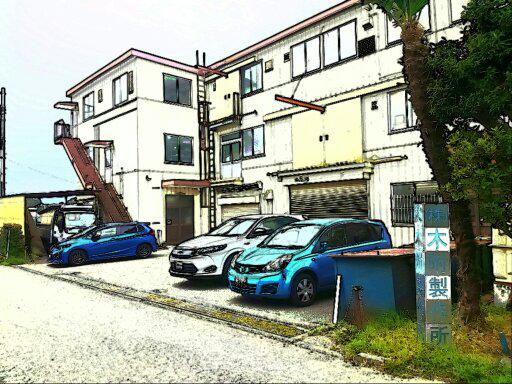
え~
本日は1日現場にいたのでブログ更新は無理かな~と思ったのですが
出来る時にはやっておこうかなと帰宅後に更新しております('◇')ゞ
年度も変わり、新年号になろうとしていますが
みなさん、そろそろ慌ただしくなってきたのではないでしょうか?
当社は少人数の会社なので
忙しくなってくると全員が仕事を掛け持ちして回します。
ですが、個々が得意分野を無駄なく持ちまわるので
大人数の会社に負けず劣らずの力を発揮します!(これ本当)
(忙しくなると普段温厚な御年〇〇歳の職人さんも含め
『えっ!!誰⁇』と思う位みんなスーパーサイヤ人みたくなります(笑))
例としてあげると・・・
【検査主任のS氏】
メインの仕事はもちろん『完成品検査』です。
鋭い眼光で小さな不良も見逃しません!!
(時にはこれ位見逃して~と思う事もあります(*´з`)←ダメな奴)
完成品検査の他にも、
実際に加工に入る前に展開後のCAD図を見て
穴数や穴径、外形や展開長が合っているかの事前検査も行います
(これ結構重要!)
事前検査で不良が未然に防げれば
材料を無駄にしなくて済みます。
当方は自分で展開した品物の中で
『これを間違えたら取り返しがつかないなぁ』と思う
大型の品物などをCAD図やホールチャート
(穴数や穴位置、穴径などを記した表)を
S氏に提出し検査してもらい『OK』が出てから抜きに回します。
S氏は時には『タレパン』のオペレーターでもあり
自分で抜いた何百個もの品物を
物凄い勢いでバリ取りしてタップを立てたり皿をもんだり
リーマーを立てたりと慌ただしく働いております。
手先が器用なので『ちょっと自社では厳しいんじゃない?』
みたいな追加工や、機械加工に近い繊細な加工もこなします。
(これには当方も感服しております(;'∀'))
会社イチの力持ちでもありSUSの3㎜メーター板(50㌔弱)を
1㎜の板かのように『ヒョイ!』と持ち上げます(^^;
4㎜(63㌔位)まで持って歩いてるの見たことあります(^^;コワイ
当方(一応女性)は2㎜の板(30㌔強)を持ち上げるのがいっぱいいっぱい…
(頑張れば以前は2.5㎜(40㌔弱)まで持てましたが最近はチャレンジしてません(^^;)
自分がレーザーを担当する時などは
S氏に3㎜を乗せてもらったりしております(^^;
(いつもすいませんm(_ _;)m)
その他の人達も色々やっているのですが
一回で書ききれないので追々紹介いたします!
さて
現場が落ち着いてくると
今度は納品準備が忙しくなります。
これも専任が居るわけではなく
普段は事務処理や受注管理をしているIさんや
営業責任者のKさんが兼務してこなしているのですが
一日の納品が何百点にもなる事があると、
とうてい追いつきません。
納期に間に合わなくなったら大変!!
せっかく当社を指名して仕事を任せてくれたお得意様に
絶対に迷惑はかけられません!
そうなると工場長の号令で
現場を止めて全員で納品準備に回ります。
会社は小規模かもしれませんが
『ものづくり』に対する情熱とプライドは大手に負けていないと自負しております!
☆彡少数精鋭!職人集団!木附製作所!!☆彡
これからもよろしくお願いいたします!!
…あ!
もう日にちが変わってしまったのでこの辺で(^^;)
明日(今日)も仕事頑張るぞ~(=゚ω゚)ノ
【オマケ】
★板金屋 哀歌★
『「コストダウン」 応えたいけど 無情にも 上がる材料、人件費!』
近年、材料の高騰が続いておりますが、
企業努力&VA提案でコストダウンの希望に
出来るだけ添えるよう頑張るしかない!
中小企業の皆様!
日本の『ものづくり魂』の火を消さないように
共に頑張りましょう( `ー´)ノ
投稿: 2019/04/05
ブランク系(抜き、成形)の機械
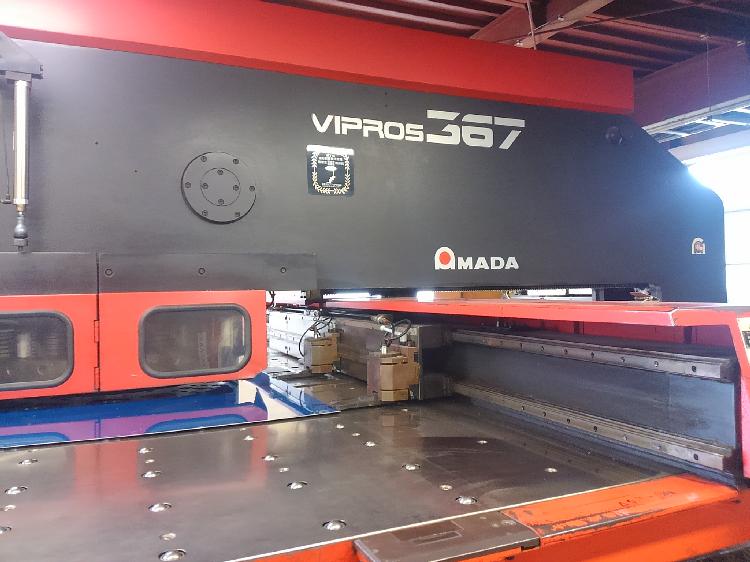
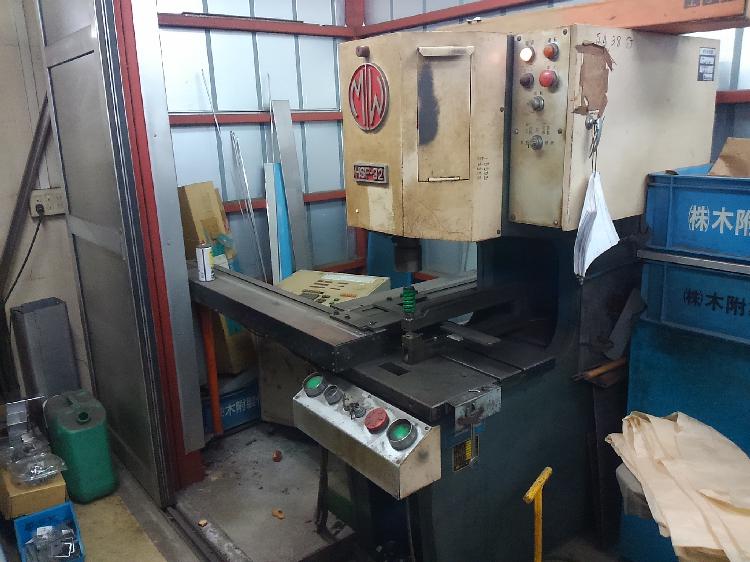
今日は、展開とデーター出力の仕事が溜まっていて
現場に作業風景を撮りにいけないので
撮り貯めておいた写真の中から
自社にあるブランク系の機械を簡単に説明します。
最初の写真は通称『タレパン』と呼ばれるタレットパンチャー
AMADAのVIPROS367です。
本当は5×10材まで加工出来る機械なのですが
配置位置の関係で当社では5×8材(1524×2438)までの加工になります。
板厚的には鉄やボンデ等なら0.6~3.2㎜、ステンレスなら2㎜
アルミや銅なら6㎜位まで。
主にレーザー加工に向いていない
ビニール貼りの研磨材や銅製品の加工、
バーリングやルーバー等の成形加工で活躍しています。
金型ステーションには58種類の様々な型をセットできるので
レーザー程ではありませんが割と複雑な形状の物でも加工出来たりします。
一旦型をセットすれば、レーザーよりも圧倒的に加工速度が速いので
量産品の加工でも重宝しています。
次の写真は『セットプレス』です。
主に小物部品のブランク加工を行うための機械です。
タレパンと違って金型は1つしか入らないので
うちではレーザーやタレパンでは困難な追加工等で使っています。
加工する穴や切り欠きに合った金型をセットプレスに取り付け
寸法を入力し、材料を突き当てに合せて位置決めを行いながら加工します。
最近では稼動しているところをあまり見かけませんが
たま~に『セットプレス』じゃなきゃ加工は無理だ!!
みたいな事もあるので大事に置いています。
・・・この2台の機械、実は当方の入社以前から置いてあるので
いつ頃導入したのかなど詳しいことはわかりませんが、
名称を元に製造年式を調べたところ
『タレパン』が大体1999年(平成11年)で約20年物!
『セットプレス』が1988年(昭和63年)でなんと31年物!!!
だということがわかりました\(◎o◎)/!!
いや~結構な年月が経っていますがまだまだ現役!!
バリバリ活躍しております!!
さて、当方も図面が山盛りになってきたので
機械に負けないように頑張って働きます(・へ・)!!
【オマケ】
★今日の板金屋標語★
『20年 古い機械と言うけれど 人間ならば まだハタチ!』
・・・
と言う事でこの機械達、
うちの職人さん達よりも まだ若い‼(笑)
そんな訳で、まだまだ頑張ってもらいますよ~!!
では今日はこの辺で!
投稿: 2019/04/04
今日の1コマ エルボー型ダクト溶接
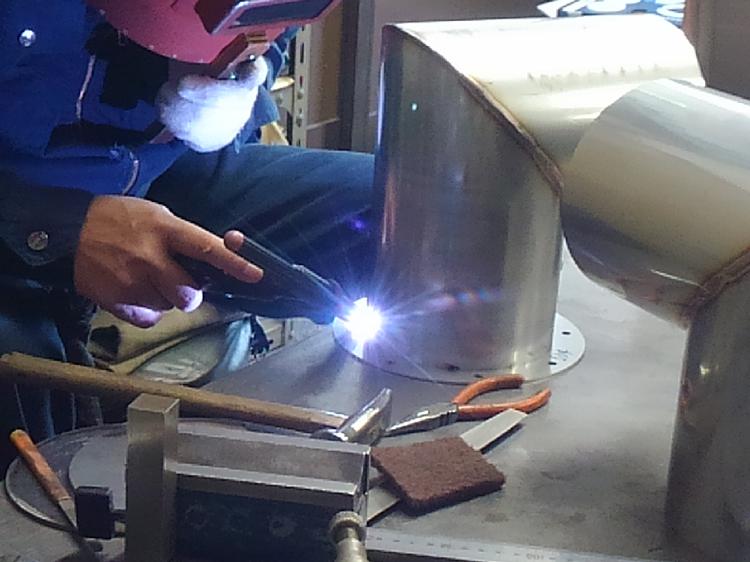
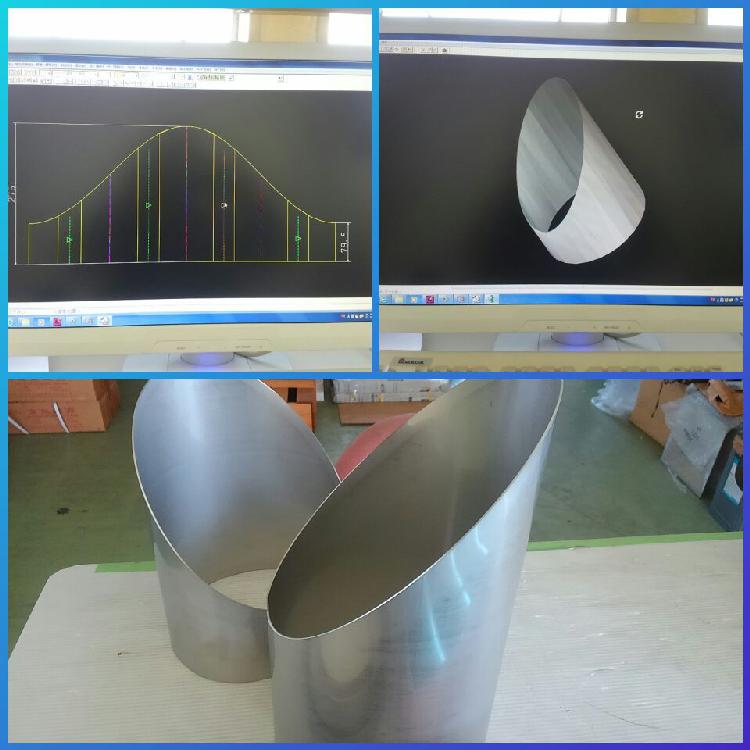
溶接班 班長O氏がエルボー型のダクトを溶接していたのでパシャリ!
もう一枚は溶接前の写真です。
左上から2D(平面)展開図、右上は3D立体図、下が丸めた後になります。
この形になるまでの工程も紹介したかったのですが取り損ねました(-_-;)
平面板から筒状にするのに、
まずは両端をR曲げの要領でベンダーでハナ曲げして
そこからローラーに通してクルクル回して丸めていきます。
寸法見ながらを少しずつ圧を強めて、内径のゲージと合せていくので
ピッタリ合せるのは結構時間がかかります。
この工程で圧が強すぎて丸めすぎるとφ径が小さくなってしまい
接続面も合わなくなってしまいます。
そうすると溶接班からクレームが来ます・・・^^;
ある程度綺麗に丸まっても
溶接の時に熱が加わることで引っ張られてしまい
形が崩れてしまう事もあるのですが
そこは品物にお灸を据えたり、部分的に叩いたりと、
職人技でうまく修正していきます。
このダクトは『水密』の指定があるので
『カラーチェック』と呼ばれる水漏れが無いかの検査をします。
漏れが有った場合にはそこの箇所を溶接し直して
再度カラーチェックです。漏れが無ければ
寸法、真円度を検査して酸洗いに出して完成です!
【オマケ】
★板金屋あるある パート2★
『品物を 持って近寄る検査員 一瞬全員 目をそらす!』
・・・
品物の完成検査を担当する人が
見覚えのある品物を持って近づいてくると
誰もが
『こっち来ないといいな・・・^^;』
『あれっ??・・なんかおかしかったかな(・・;)』
『なんか間違ってたかな(ーー゛)??』
と、一瞬心がざわつくものです・・。
自分の後ろにぴたりと止まった時には
『ゴチになります』で最後に肩を叩かれた人の様な気持ちになります(=_=;)
不良品は出さないのが大前提ですが、
たまーに図面の見落としや気の緩みでやらかしてしまう事もあります。
それを社外に出さないようにしてくれる『最後の砦』検査員!!
誰しも自分の不良を指摘されると
落ち込んだり嫌な気持ちになりがちですが
『社外に出る前で良かった!』『検査員さんありがと~』
『次からもっと気をつけよう!』と前向きな気持ちに切り替えて
明日も頑張りましょう!!
では今日はこの辺で!!
投稿: 2019/04/03
今日の1コマ 125tベンダー長物曲げ
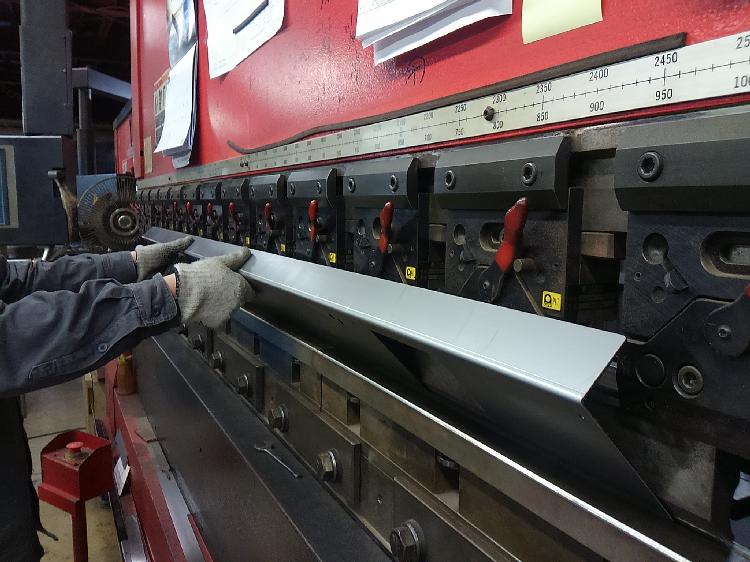
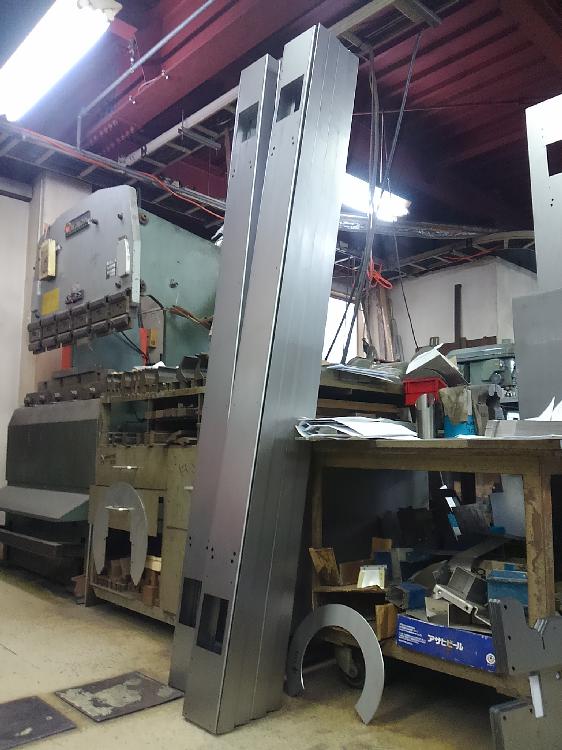
ブログを開始するに当たりテストも兼ねて
今日の作業の一部をご紹介します。
特段変わった加工が無い日でも
何気ない作業等アップしていきますので
暇つぶしにでも見に来てください!
なんかネタは無いかな~と現場を物色していると
工場長が2メーターのブラケットを曲げていたのでパシャリ!
長物は溝も型も1本では加工できないので
慣れていないと角度がバラついて通りが出ないのですが
さすがはベンダー歴ウン十年のベテラン!
一発で決めてました!さっすが~!
おおっと、サボってる疑惑の視線を感じたので
そそくさと撤収・・・
ちなみにこちらのベンダー、3メートルまで曲げられます
(板厚にもよりますが・・・)
今日曲げていたのはSPCCの板厚2㎜の品物です。
この後ウェルドナットを溶接してメッキをかけて完成です!
【オマケ】
★板金屋あるある★
『品物を 完成させた翌日に 同じ図面がまた手配!』
標語風にしてみました(笑)
タレパンやベンダーの型をそっくり変えてしまった瞬間に同じ品物の図面を持っていくと、
職人さんたちはしばらく固まって動けなくなる習性があるようです(^_^;)
同業の方なら『あるある』とうなづいて頂けると思いますが・・・^^;
まあ、注文が繰り返しあることは喜ばしい事ですよね!!
では今日はこの辺で!
投稿: 2019/04/02